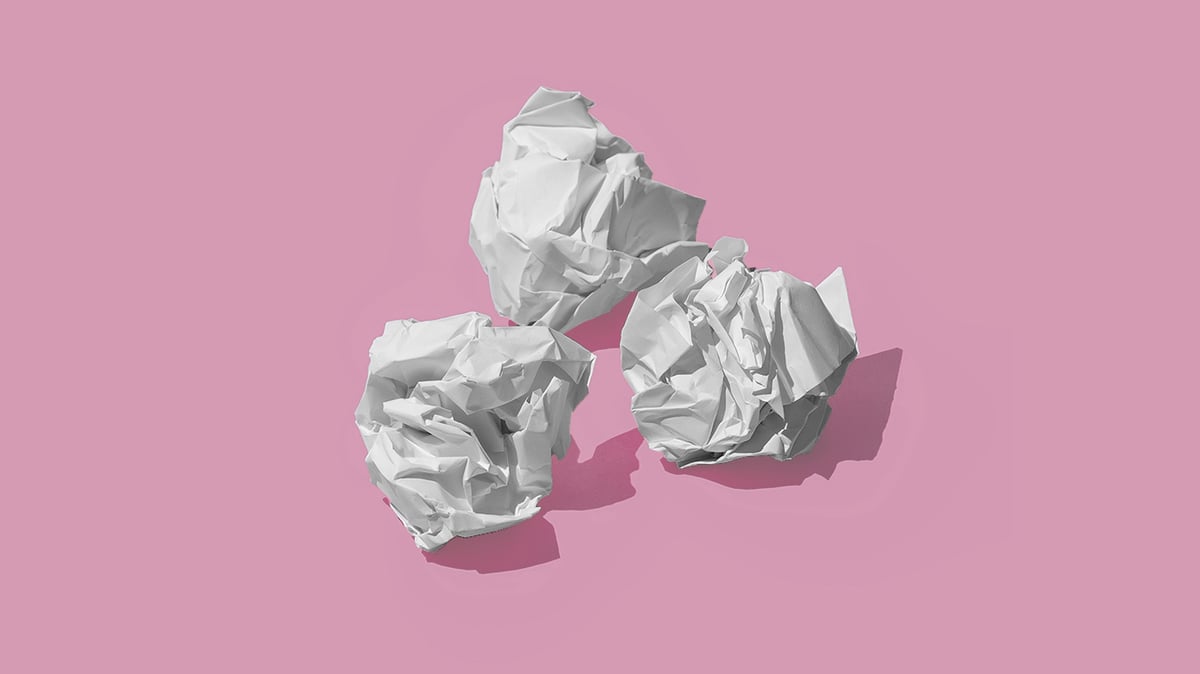
In the world we live in today, mass production of goods and industrial development is on the increase and the economy thrives on the capability of countries to export to other countries for profit. These production companies comprise of different departments that work collectively in ensuring productivity is continuous and efficient. Hence, it is important that no matter how sophisticated the production process may be, certain standards and quality of the product must be attained to constantly meet the company’s targets.
The importance of a QMS
in your organization
Quality management refers to a set of systemic operating procedures that are well established to ensure that the requisite standards are maintained for effective quality delivery and ensure customer satisfaction. A quality management system (QMS) is therefore required by businesses and companies because it helps them to focus on consistently meeting certain standards of production and customer requirements by seeking to enhance their satisfaction.
The mind behind the creation of the term “Quality Management System” was Ken Croucher who worked in 1991 as a British management consultant. He developed the acronym QMS and oversaw the design and implementation of a QMS within the IT industry. The basic Quality Management process involves companies and organizations seeking compliance or certification to establish the procedures involved in the production, the sequence and interaction of these processes. Some of these processes may include order processes, production plans, service/process measurements, calibrations, internal audits, corrective actions, preventive actions, identification, labeling and control of non-conforming products to prevent its inadvertent use, purchasing, and other related processes.
The most commonly adopted quality management system standards are the ISO9001. It is the international standard specifying requirements for quality management systems. It is designed to help organizations ensure that they are able to effectively improve their customer satisfaction and that of the board while also ensuring that certain standards are maintained in the production of certain goods or services.
From paper-based QMS to eQMS
Technology in the 21st century is advancing at rates too fast for the average human eye to keep up. With this advancement in technology comes a transition from the tedious paper-based Quality Management Systems to the more advanced Electronic Quality Management Systems. Paper-based quality management systems used to be very common in medium-sized organizations. Such systems can successfully manage product and process quality, no doubt about that. However, they significantly increase the risk of cGMP non-compliance at the FDA-regulated organization. That is just one of the many disadvantages that come with using a Paper-based Quality Management System. It’s no longer news that anything with the name tag “electronic” is probably going to be more efficient and effective, and that is exactly what you get with an Electronic Quality Management system.
Quality systems are complex and extremely difficult to manage across an entire organization, especially in regulated environments where strict adherence to quality standards is required. Hence, companies and organizations seeking to enhance their businesses quickly look to adopt software-based Quality Management Systems. Below are 8 of the main advantages Electronic Quality Management Systems have over the traditional Paper-based Quality Management Systems:
1. Connecting the Organization
One major role a Quality Management System plays is to link the different departments in an organization together. The use of paper-based QMS might help to widen the gap for quality system collaboration between the different sections in an organization. Thus makes quality integration tedious. However, all that is trumped by the delicate infrastructure of an Electronic Quality management system. It allows for seamless inter-department communication to facilitate quality production.
2. Better and Advanced Data Management
Using an Electronic Quality Management system allows the possibility for real-time management of all recorded data. In order to meet up with industry standards and guidelines, you require Corrective and Preventative Actions (CAPA), Change Control, Deviations, and Complaints, to record data history.
3. Faster and Better Accessibility
Working with a Paper-based Quality Management system has the disadvantage of having restricted storage and access, which is often violated with no documented record of changes made or by whom. However, an Electronic Quality Management system ensures that it is quite easy to access records anywhere you go by simply having the required access codes and an internet connection. It ensures that record retention policies are adhered to and retrieval of records more efficient.
4. Eliminate waste
One of the obvious benefits of an electronic quality management system that every environmentalist will agree with is the effectiveness in saving paper and reducing waste. Most notably, the implementation of an electronic quality management system saves time.
5. CAPA management
In a paper-based system, it is difficult for quality managers to implement continuous improvement initiatives. The lack of a reliable closed-loop control makes it difficult to implement corrective actions. Because of this, it is nearly impossible to ensure that standards are not compromised.
6. Document Control
In a paper-based environment, the review cycles can be long and unpredictable and paper-based document control procedures can also be more error-prone. Such issues could compromise an organization’s compliance with regulations and make it difficult to implement improvement initiatives in a timely and predictable manner.
7. Metrics
It’s a no-brainer that paper-based systems make it very difficult for companies to collect and review key operating metrics in a timely manner. But with an Electronic Quality Management System, data can be retrieved almost as quickly as they’re needed, and operating metrics can be easily accessed.
8. High Cost of a Paper-based Environment
It may seem that a Paper-based QMS is inexpensive to maintain. However, there is a huge amount of hidden costs due to the enormous amount of time the organization spends to ensure correct management of such a system. With an Electronic Quality Management System, you cut down costs in the long run.
The conclusion is that eQMS has quite a few advantages over traditional QMS implementations which cannot be ignored by companies who take quality management seriously. Even a digital QMS which only replaces paper by scanning it, is missing most of the eQMS advantages. Therefore, the question is not if a company should switch to an eQMS but when.
If you want more information or if you would like to see a demo of our Scilife eQMS solution which includes all of the aforementioned advantages, please contact us.