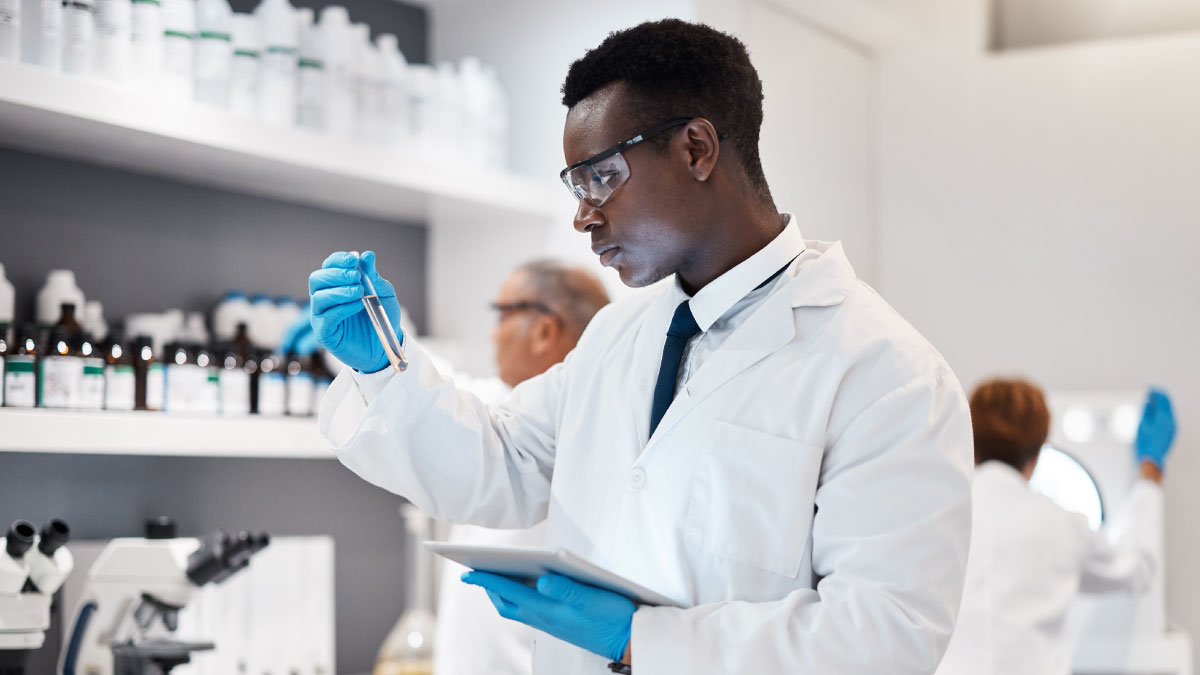
The objective of a QMS is to define and formalize a system that documents processes, procedures and responsibilities for achieving quality policies and objectives. It basically provides the structure for various functions within an organization to work in an integrated manner, for delivering the best quality products and services to the customer.
What is a Quality Management System in Life Sciences?
A Quality Management System in life sciences is a regulatory and quality blueprint. It documents the processes, procedures, and responsibilities required to maintain and exceed the industry's stringent standards. A QMS is not just a framework but the very essence of operational excellence in life sciences.
One can refer to ISO 13485:2016 or ISO 9001:2015 to know the benchmark for meeting international standards for Quality Management Systems. Apart from these International Standards, EU and US regulatory agencies also require manufacturers to meet QMS requirements. EU agencies have published EU MDR and EU MDD for manufacturers to understand the infrastructural requirements for QMS. Whereas 21 CFR Part 280 of Federal Regulations is explicitly dedicated to ‘Quality System Regulation’.
Why a Tailored QMS Matters in Life Sciences
The life sciences industry stands as a pillar of innovation and reliability. QMS is not just about adhering to standards; it is about embedding quality into the DNA of every product and process. It embodies an integrated network of processes, responsibilities, and procedures, meticulously designed to uphold stringent regulatory standards and deliver superior quality products consistently. It is the structured way organizations can not only meet but anticipate the needs of both regulatory agencies and customers.
As we navigate through this complex terrain, we anchor our discussion on a hypothetical yet revolutionary digital solution, Scilife. This solution encapsulates the full spectrum of QMS capabilities. With modules catering to every critical aspect—from document control to CAPA (Corrective and Preventive Actions) management —Scilife exemplifies the seamless unification of process efficiency and compliance rigor.
Plan-Do-Check-Act
At the heart of an effective QMS is the Plan-Do-Check-Act cycle, a concept popularized by Dr. W. Edwards Deming. This iterative process ensures continual improvement and operational excellence. If you are a quality professional, you will definitely agree that nothing can make things simpler than Deming's Plan-Do-Check-Act. Let us keep the lengthy texts in the standards and regulations aside for a while to understand the essentials of Quality Management with an easier explanation.
Plan: Establishing a Robust Foundation
Planning is the first step in everything we do, and naturally for the Quality Management System too. In this step, you should plan and document your quality policy.
The planning phase is the blueprint for quality. It involves the development of a comprehensive quality policy that outlines the objectives and the structural methodology to achieve them. Essential documents—procedures, work instructions, and templates—form the backbone of this stage. In the digital era, this often translates to cloud-based solutions that provide agility and traceability, ensuring critical information is secure and accessible.
A quality policy should contain organizational processes that enable an organization to achieve its Quality objectives.
In order to meet the quality objectives in your organization, you will need a set of standard operating procedures, processes, work instructions, designs, forms, and templates.
What will happen if your organization fails to have a documented quality policy, procedures, processes, work instructions, forms, and templates?
The first infrastructure element that your organization will need to build a QMS is documentation. Traditionally organizations relied on paper-based documents but owing to tremendous technological progress, nowadays organizations are opting for more advanced cloud-based documentation platforms.
Imagine you have a cloud-based documentation platform and all your quality policies are documented on it, then the question arises, is it enough? The answer is no. There are many Document Control requirements that life science manufacturers must meet as defined by 21 CFR Part 11 and EU Annex 11.
While it is possible to exercise document control manually, automating it takes out a huge amount of burden from the shoulders of scientists. ‘Document Management’ is the first essential element of a Quality Management System. Scilife’s Document Control Module automates the entire document management workflow.While it is possible to exercise document control manually, automating it takes out a huge amount of burden from the shoulders of scientists. ‘Document Management’ is the first essential element of a Quality Management System. Scilife’s Document Control Module automates the entire document management workflow.
Do: Execution with Precision
With the planning stage complete, the execution takes center stage. In this step, the documented procedures are brought to life. In the digital age, cloud-based systems offer seamless adherence to procedures across the globe, maintaining consistency.
Execution starts when everything is perfectly planned. At the ‘Do- stage’, there is very little for the QMS to do. It only serves as your guide for execution. The regulatory agencies demand that you ‘do what you say and say what you do.’ The onus here is on the doer in this case. The documented procedures, processes, and work instructions are not going to change without going through an approval process. Therefore, the doer must abide by the written procedures.
Check: The Pulse of Compliance
The 'Check' phase is a proactive stance on quality assurance—regular audits, meticulous monitoring of processes, and the swift handling of non-conformities. Automated solutions like Scilife’s Audit and Events Modules have revolutionized this phase, allowing real-time oversight and response, which is paramount to upholding the integrity of the QMS.
Doing is not enough, we must check the conformance with documented procedures. The checking stage is usually performed during regular QA approvals and audits. In a way, audit processes are the second essential element of Quality Management Systems. The audit Module in Scilife automates these processes.
In the event of a nonconformity or customer complaint, you are expected to acknowledge and address the issue. Often, this is followed by a root cause analysis to identify areas for improvement. As a result, event handling processes are the third essential element of a Quality Management System. With Scilife's Event Modules, you can also automate this process.
Act: Embracing Continuous Improvement
In this crucial last phase, 'Act,' we dive into the data gathered during the 'Check' phase to identify and implement corrective and preventive actions. This phase is all about embracing continuous feedback, which not only keeps our QMS up and running but also constantly evolving and enhancing. Once we pinpoint areas needing improvement, the next step is straightforward: address the root causes head-on with corrective and preventive measures.
The Building Blocks of a Life Science QMS
- Implement a Quality Management System
- Ensure compliance with regulations
- Manage Supplier’s Quality Assurance
- Implement Quality Control Measures
- Continuous Improvement
1. Implement a Quality Management System
QMS is built on four pillars:
- Quality Objectives and Policies
- Quality Manual
- Procedures for Document Control and Record Keeping
Each of these elements is customized to align perfectly with the regulations of the life sciences industry. While Quality policy is a declaration of your organization's unwavering commitment to quality by laying the groundwork for crafting the processes and procedures that will bring this commitment to life, the quality manual describes the system's framework and operations and details how your system aligns with complex regulatory requirements.
With technological advancements, especially cloud-based solutions, document control has taken a giant leap forward. Modern QMS solutions offer documentation that is secure and traceable and also readily accessible. This is a game-changer for both regulatory compliance and operational efficiency.
Scilife brings to the forefront an advanced document lifecycle management solution, complete with automated version control, audit trails, and signature capture for document approvals.
2. Ensure compliance with regulations
The QMS serves as the sentinel of compliance by ensuring that everything you do aligns with current regulations. This process can be streamlined by incorporating all regulatory requirements into the operational workflow of a QMS.
Through regular internal audits, a QMS not only checks the pulse of compliance but also identifies opportunities for process improvement and risk mitigation.
3. Manage Supplier’s Quality Assurance
Having a robust Quality Management System extends its reach to suppliers. You can establish a comprehensive Supplier Quality Assurance by creating the below processes to ensure that input quality matches output quality. Additionally, audits and supplier related metrics are a crucial element of a supplier QMS as they ensure that every link in the supply chain is strong and compliant and supplier performance aligns with your quality objectives.
- Supplier Qualification Program
- Supplier Audits
- Supplier Performance Metrics
4. Implement Quality Control Measures
To have an effective QMS, you should implement quality control measures such as the following:
- Quality Control Plans and Procedures
- Inspections and Testing
- Statistical Process Control
These are the tactical steps to ensure products are manufactured with the highest quality. Additionally, regular inspections and rigorous testing in process steps validate the efficacy of your quality control measures. Again SPCs allow continuous data analysis, providing a scientific basis for decision-making.
5. Continuous Improvement
It is a commitment to continuously improve processes, products, and services. It can be performed with the following:
- Continuous Improvement Programs
- Data and Metrics to Drive Improvement
- Culture of Continuous Improvement
Typically, processes in the life sciences industry have a data-rich environment through inspections, tests, controls, SPCs, so that you can leverage the data and metrics for improvement. By doing this, you can achieve informed decision-making and strategic enhancement. The organization’s culture is also a vital element of continuous improvement as quality is not only the quality department's responsibility, but a collective mindset. It should be an environment where all employees are empowered and motivated to seek out and implement improvements.
Conclusion:
Envisioning the Future of Flawless Quality Management
As we embrace the future, QMS remains important for ensuring the safety, efficacy, and reliability of life sciences. However, the tools we use and the strategies we deploy are continuously evolving. This is a leap towards sustainability, innovation, and quality at the heart of all life sciences endeavors.
Deming’s Plan-Do-Check-Act cycle makes it very easy to break down essential elements of Quality Management Systems.
These components can be interlinked together in Scilife to give a full picture of the Quality Management Practices followed within the organization. The cloud based software solution eliminates the need to invest in large physical infrastructure and trained workforce for maintenance of the infrastructure.
Scilife's comprehensive suite demonstrates a shift towards a more efficient, transparent, and connected quality management ecosystem. The challenge of compliance can be turned into a competitive advantage, so you can ensure your commitment to quality endures for as long as your life-saving products do.
For a better understanding of Scilife's transformative potential, we invite you to schedule a personalized demonstration with our specialists. Embrace the future of quality management in the life sciences today.