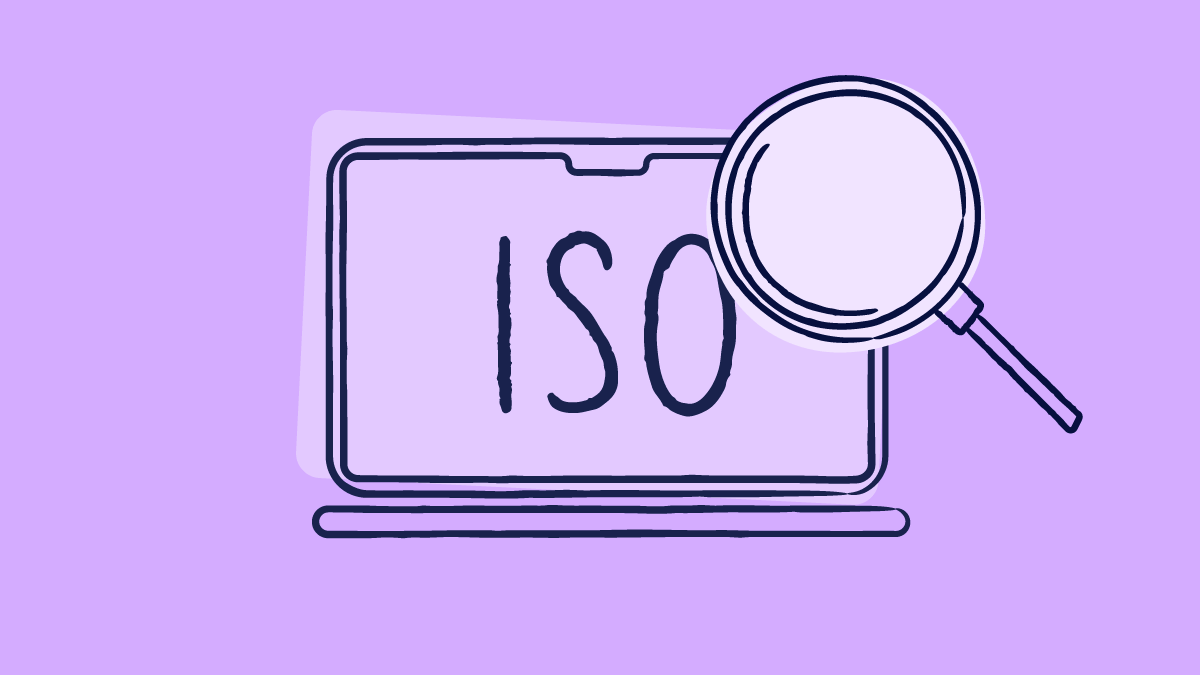
Getting through an ISO audit is one of the most important defining moments for any life sciences company. Whether you’re manufacturing pharmaceuticals, developing medical devices, or working in biotech, these audits are how regulators and customers confirm that your processes meet internationally recognised standards like ISO 13485 or ISO 9001. Audits give structure to your Quality Management System, but they can also expose gaps if your documentation, training, or procedures aren’t up to scratch.
In this post, I’ll break down exactly what an ISO audit is, what can go wrong, and what the consequences of a failed audit look like. I’ll also walk you through the most common mistakes I’ve seen quality teams make and share practical tips to help you avoid them. If you’re new to ISO audits or just want a better way to prepare, this guide will help you feel more confident when it comes time for inspection.
What is an ISO audit?
An ISO audit is an official review of your quality system to check whether it meets the standards set by the International Organization for Standardization. It is carried out by a qualified external auditor or certification body.
These audits are particularly important for companies working in regulated industries, like life sciences, where products affect patient health and safety. Depending on your focus area, the relevant standard may be ISO 13485 for medical devices, ISO 9001 for general quality management, or ISO 15189 for medical laboratories.
There are different types of audits, too. First-party audits are internal, second-party audits involve external stakeholders like suppliers, and third-party audits are the formal audits done for certification or recertification. For life sciences companies, these external audits are where your QMS is truly put to the test.
What happens if you fail an ISO audit?
Failing an ISO audit can have a lasting impact on your business. For life sciences companies, the consequences go beyond a failed inspection report. Without a valid ISO certification, such as ISO 13485 or ISO 9001, you may be blocked from entering regulated markets, lose existing customers, or become ineligible to supply to partners who require certified vendors.
Beyond market access, audit failure usually triggers a Corrective Action Plan. This means your team will need to investigate the issues raised, make the necessary changes, and provide documented proof that the problems have been resolved. Depending on the severity of the findings, this can lead to unplanned costs, tighter timelines, and a major resource drain across departments.
If serious or repeated gaps are found, regulators may require more frequent follow-up audits. This increased scrutiny not only places pressure on your quality teams but can also delay product launches, trigger recalls, or result in warning letters. Even when the issues are addressed, a failed audit can shake internal confidence and slow down momentum in the business.
Most companies do not realise how disruptive a failed audit can be until they are in the middle of one. The time, effort, and cost of a corrective action is nearly always greater than the effort it would have taken to prepare properly in the first place.
The 10 most common ISO audit mistakes
Over the years, I’ve seen the same issues surface during audits, even in well-run companies. These mistakes are easy to miss but can cause real problems if left unchecked. Below are ten of the most common, with quick guidance on how to avoid them.
Poor document control
Audit issues often start with documentation. If procedures are outdated or teams are using different versions, it creates confusion. Keep one controlled version of every document, make sure changes are reviewed and approved, and confirm that everyone is working from the same source.
Weak CAPA processes
Corrective actions should go beyond surface fixes. Auditors expect clear root cause analysis, timelines for action, and follow-up to show the issue was resolved. A vague note saying "staff retrained" is not enough without details and supporting evidence.
Missing training records
You need to show that staff were trained on the current version of a procedure before they performed the task. That means having time-stamped records with names, dates, and the specific material reviewed.
Limited management involvement
Quality is not just the responsibility of one team. Auditors want to see that leadership participates in regular reviews, sets goals based on quality data, and supports improvements when issues are raised.
Unclear risk management
Risks should be identified, documented, and linked to controls at every stage of the product lifecycle. Your audit should be able to show what risks were considered, what actions were taken, and how those decisions were tracked.
Incomplete supplier oversight
Suppliers who affect product quality must be qualified and monitored. Keep records of audits, certifications, complaints, and performance reviews. It should be easy to trace supplier impact back to your quality data.
Manual workarounds
Spreadsheets and offline files can work in a pinch, but they introduce gaps. If critical processes live outside your QMS, traceability suffers. Bring essential workflows into the system so nothing is missed or overwritten.
Gaps in audit trails
Every change made in the system should leave a clear path. That includes who initiated it, who approved it, what was changed, and why. Missing pieces create doubt and force auditors to ask more questions.
Treating audits as one-time events
Preparing only when an audit is due creates panic and inconsistency. A strong quality system should be ready all year round. That way, audits feel like a review of ongoing work, not a last-minute rush.
Repeating the same issues
If you are flagged for the same problem in multiple audits, it shows that lessons are not being applied. Keep track of previous findings, verify that actions were closed properly, and revisit those areas regularly.
Key takeaways
- ISO audits confirm whether your quality system is aligned with international standards and consistently applied across your organization. In the life sciences space, this directly affects your ability to deliver safe products, retain customer trust, and meet regulatory expectations.
- Failing an ISO audit can lead to serious consequences. These may include certification loss, delayed product launches, increased audit frequency, and reputational harm. It can also create internal pressure and pull focus from strategic work.
- Most ISO audit failures are avoidable. Weak CAPA records, outdated SOPs, poor document control, and a lack of evidence for training are recurring issues. Addressing these early makes a major difference during an audit.
- Quality is everyone’s responsibility. The most successful companies prepare for audits by embedding audit readiness into their daily operations. This includes regular internal reviews and strong management involvement.
- Technology can support audit readiness. Using an eQMS like Scilife helps centralize quality processes, making it easier to keep documents, training, CAPA, and audit trails consistent and inspection-ready at all times.
- Audits provide a chance to strengthen internal processes and spot weaknesses before they cause bigger problems. When teams understand the common issues and take action early, they can create a more reliable system and support long-term improvement.
Conclusion: How to prepare for an ISO audit
If I could give just one piece of advice for preparing for an ISO audit, it would be to treat audit readiness as an everyday activity, not a last-minute scramble. Build structure into how documents are managed, make sure training records are complete and up to date, and check that corrective actions are more than just paperwork. Use internal audits to simulate the real thing, and involve leadership in reviewing the data and driving improvement.
Tools like Scilife’s eQMS can make this much easier. Connecting your quality processes into one platform will reduce the risk of things falling through the cracks. Documents, training, CAPA, audits, and supplier records are all linked, searchable, and ready when you need them. That means when the auditor arrives, you’re not scrambling. You’re showing them how your team already works. That confidence can make all the difference.