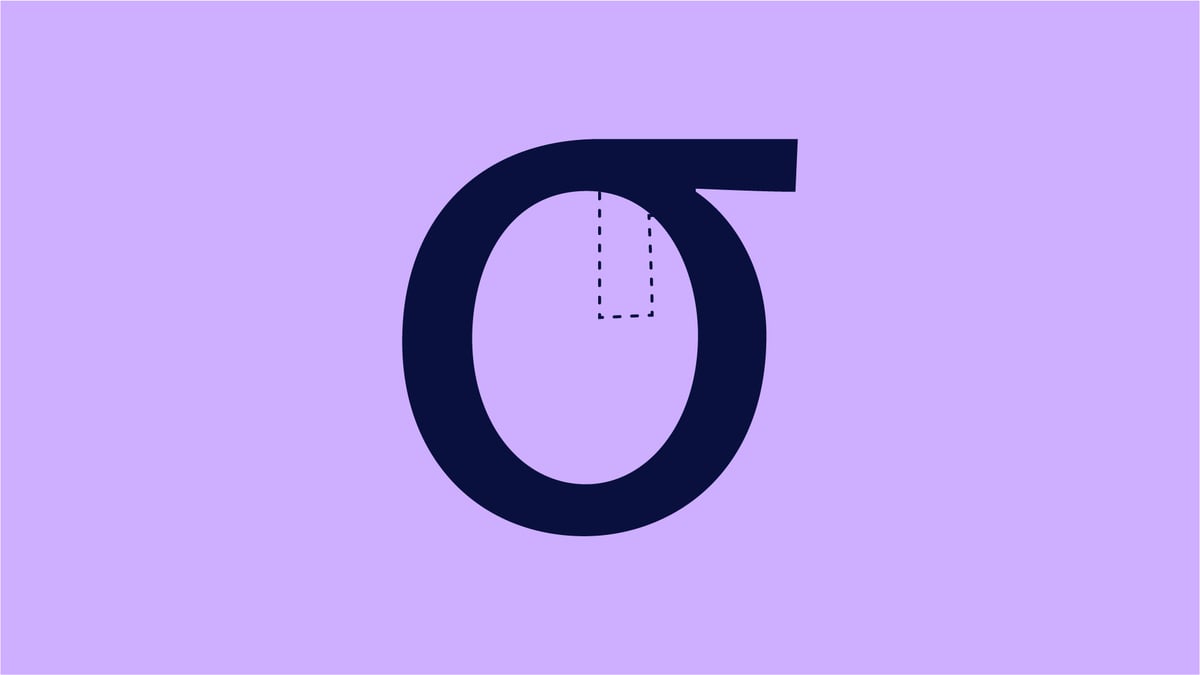
What is Lean Six Sigma?
As the name suggests, Lean Six Sigma is a business management strategy that combines principles of Lean manufacturing and Six Sigma.
Lean focuses on the removal of wastes (wasteful activities known as ‘Mudas’), and Six Sigma focuses on the reduction of variation in quality. Hence, Lean Six Sigma works by improving business performance by systematically removing waste in addition to reducing variation.
History of Lean Six Sigma
The first strategy to emerge was Lean. The use of Lean can be traced back to the medieval era, but the first person who integrated the concept of lean into the manufacturing system (with stunning success) was none other than Henry Ford. In later years, during World War II, Toyota created the 'Toyota Production System' with inspiration from Ford's work. Lean is basically a legacy of the automotive industry.
Fast forward 50 years, and Motorola is creating history with Six Sigma. The company successfully implemented this strategy to measure and reduce defects per Million opportunities. As a result, Motorola recorded $ 16 Billion savings and bagged the Malcolm Baldridge National Quality Award in 1988.
Eventually, Lean Six Sigma evolved in 2001 when a book titled Leaning into Six Sigma: The Path to Integration of Lean Enterprise and Six Sigma by Barbara Wheat, Chuck Mills, and Mike Carnell was published.
To summarize, Lean flourished in the early years of the 19th Century, Six Sigma grew in the later years of the 19th century, and the combined Lean Six Sigma approach was birthed in the 20th century.
How are Companies using
Lean Six Sigma?
Companies use Lean Six Sigma to fulfill the following objectives:
-
To limit the number of unproductive steps in an operational process. There are several lean tools used for this such as:
-
- 5s: helps to keep workspaces orderly.
- Value Stream Mapping: helps to identify wastes and waste sources.
- Gemba: useful to expose process defects.
- Kanban: helpful to manage inventory levels.
- 5s: helps to keep workspaces orderly.
-
Additionally, companies use the Design, Measure, Analyze, Improve, Control (DMAIC) framework defined in Six Sigma, which helps achieve low-defect continuous processes.
- The Define step requires analysis of goals and deliverables with set target Key Performance Indicators and timeframes.
- The Measure step collects quantitative and qualitative data from individuals participating in the business processes.
- The Analyze step draws conclusions from variable and critical quality attributes (CQAs) understood to produce causation.
- The Improve step uses causations understood from the Analyze step to set up new actions and procedures. This can involve process validation, equipment modification, and workforce adoption effectiveness, evolving with constant tweaking.
- Finally, the Control step helps ensure that the new processes are sustainable and reproducible.
- The Define step requires analysis of goals and deliverables with set target Key Performance Indicators and timeframes.
Is Lean Six Sigma a
Good Fit for the Life Sciences?
In short, the answer is both yes and no. After all, any business management strategy is only as good as the expertise and knowledge of its implementor(s). Therefore, we can say that performance is dependent on the competence and motivation of the stakeholders. Mathematically, it can be put forth as:
Performance = Competence X Motivation
The Competence and Motivation for high performance are in turn dependent on the following aspects:
- Understanding Relevance to the problem:
This is a competence-related aspect. Although Lean Six Sigma is a great strategy, it won't solve problems that are out of its scope. Therefore, it is crucial to define the scope of strategy in terms of building efficient processes that improve product quality. For example, in the life sciences industry, the Lean Six Sigma approach can reduce manufacturing costs through better management of resources, and improve quality by reducing Out of Trend or Out of Specification events. The Six Sigma philosophy is an excellent tool to build a Quality by Design masterpiece, a subject we’ve covered in detail in a previous blog article. Hence, picking up the correct problems that Lean Six Sigma can solve is the crucial step. - Team motivation:
The second factor related to performance comes down to team motivation. If the team has a high degree of motivation for not only personal success but the collective success of the group, then it will result in a better performance naturally. Team management, in turn, is influenced by the direct involvement of the top leadership. Team motivation is also dependent on the recruitment of suitable team members. Following are the essential qualities that a Lean Six Sigma team member must possess:
o Listening: Pays attention to what other team members are saying.
o Critical thinking: Can distinguish between fact and opinion. Will consider information objectively.
o Team player: Can work independently as well as with others. Is willing to join in meetings and perform routine tasks.
- Leadership involvement:
According to published research that statistically relates leadership with Lean Six Sigma vision, a leader is an efficient communicator who plays a prominent role in an employee's support and encouragement. Owing to the active involvement of leadership the employee motivation synergistically increases. A highly motivated team is bound to produce a more significant impact. The management needs to implement creative approaches to keep the team motivated.
Conclusion
A product that does not meet quality standards is a product that does not exist in the life sciences market. From the perspective of a sustainable business model, the same goes for a product without profit margins. The lean manufacturing process and Six Sigma principles complement each other very well in overcoming both these challenges.
In terms of biotech and pharma specifically, Lean Six Sigma aligns well with the FDA's PAT and Quality by Design initiatives. The data-driven techniques in Six Sigma can produce major benefits in reducing the number of experiments and prototypes required, in addition to the increased process speed and improved product quality. However, we can only experience these benefits if we use the right tool, with the right intention, at the right place, and at the right time.
Discover how a Smart QMS can help you implement a Lean Six Sigma approach in your organization.