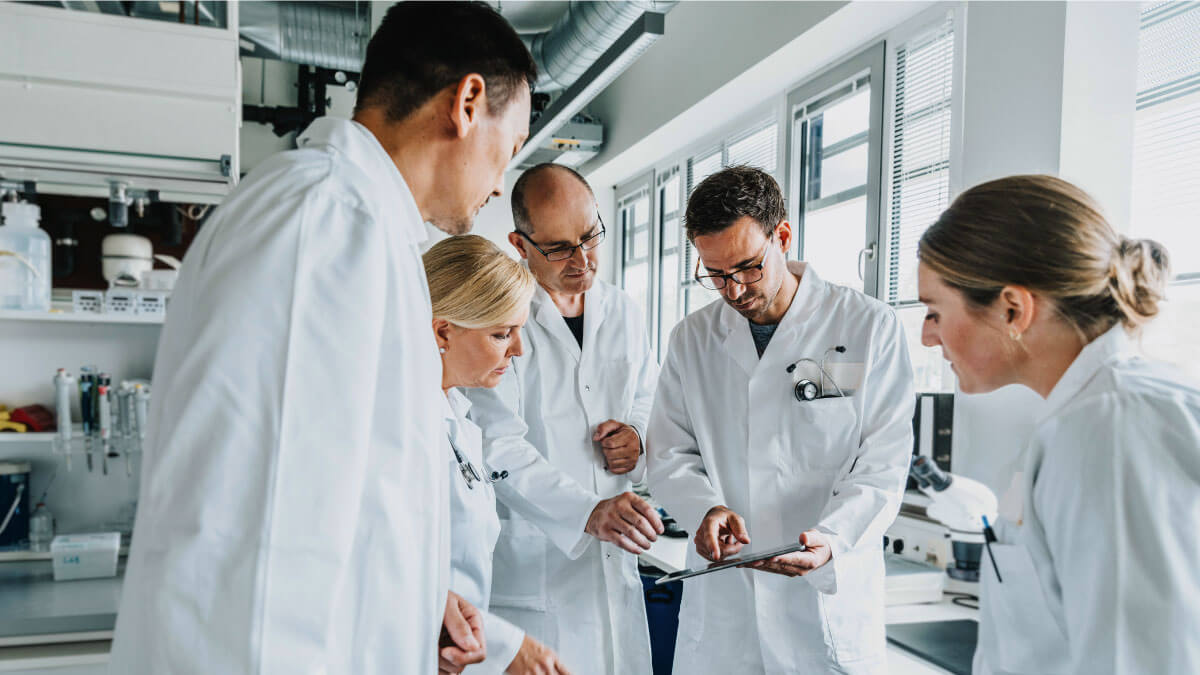
Pharma 4.0 is a framework for incorporating digital strategies into pharmaceutical manufacturing contexts. This framework envisions a manufacturing paradigm that allows manufacturers to change and iterate, connect resources and workers, simplify compliance, respond to problems with digital data, and ultimately produce more quality products with better patient outcomes.
For example, the use of electronic batch records, analytical records, digital process visibility, continuous environmental monitoring, automation of analysis, and big data analytics are just a few of the ways you can use electronic data in Pharma 4.0 in a paperless environment.
Some obstacles, however, stand in the way. The pharmaceutical industry has historically been slow to adopt new technologies, and the use of these technologies affects the role of employees and their work.
Similarly, embracing digital transformation brings about a cultural shift in organizations.
Here is a secret that we want to share with you. Pharma 4.0's success depends heavily on quality culture.
This article discusses Pharma 4.0, a technology initiative at the forefront of the pharmaceutical industry, and how to address cultural, process, and resource changes.
Takeaways
The key takeaways are:
- By embracing advanced technologies, organizations can drive innovation, increase transparency, and optimize processes.
- It is necessary to cultivate a culture of quality within organizations undergoing Pharma 4.0 implementation. This cultural shift emphasizes collaboration, innovation, and continuous learning, empowering employees to take ownership of quality processes and make data-driven decisions.
- A successful digital transformation depends on leadership commitment. It is imperative that organizations foster a culture where leaders champion digital innovation, collaboration, and continuous improvement, while also providing the necessary resources and support for employees to adjust to new technology and roles.
- Technology is the catalyst for sustained quality excellence. It enables organizations to create an agile and resilient workforce that can quickly adapt to changing customer needs and market conditions.
Pharma 4.0 Operating Model
The concept of Pharma 4.0 emerged from the broader Industry 4.0 movement, the fourth industrial revolution, which originated in Germany in 2011, as a proposal for the development of a new concept of economic policy on high-tech strategies.
In response, the International Society for Pharmaceutical Engineers (ISPE) and its members developed the Pharma 4.0 Operating Model, a roadmap for Industry 4.0 implementation in pharmaceuticals.
The Pharma 4.0 initiative applies the four principles of Industry 4.0 to Pharma 4.0
Structural Areas
There are four structural areas:
- Resources
- Information systems
- Organization and processes
- (Organizational) culture
Let's take a closer look at each structural area:
- Resources refer to the physical assets an organization has. They include people, machinery, equipment, tools, materials, and final products as well as the capabilities they use to gain a competitive advantage.
- Information systems are digital technologies that support data integrity requirements and help decision-making by connecting, communicating, and sharing information across organizational processes. These technologies include the Internet of Things (IoT), cloud data, and big data analytics.
- Organization and processes refers to the holistic framework that outlines how processes, and activities such as task allocation, coordination, and supervision are directed towards achieving the business goals.
- Organizational Culture is the collective mindset, values, behaviors, and practices that shape the way organizations and individuals approach digital transformation and data-driven approaches. Among them are organizations in which:
- Creativity is promoted to foster innovation
- People are agile and flexible in adapting to new situations, enabling rapid responses to market dynamics, technological advancements, and evolving regulatory environments.
- Collaboration creates cross-functional teams to break down silos and integrate digital technologies.
- Continuous learning is emphasized, empowering employees with skills to leverage digital tools and drive innovation.
Enablers
There are two enablers:
- Digital maturity
- Data integrity by design.
Now, let's examine the enablers in more detail: digital maturity and data integrity by design.
- Digital maturity entails a range of current digital capabilities that facilitate the successful adoption and navigation of digital transformation, new working methods, processes, and business models in Pharma:
- Digital infrastructures: cloud computing, IoT devices, data analytics platforms, eQMS.
- Smart equipment: robotics, AI-powdered systems.
- Data integration for collaboration and real-time data exchange
Digital Twins for monitoring real-time data and simulating predictive behaviors.
According to ISPE Pharma 4.0 Volume 8 First Edition, there are 5 levels to assess digital maturity in terms of Pharma 4.0:
- Level 1: Initial
- Level 2: Developmental
- Level 3: Defined
- Level 4: Managed
- Level 5: Optimized
These levels help organizations set the baseline, benchmark their maturity level against other organizations, and establish future goals. - Data integrity by design refers to the integration of data integrity controls from the initial planning of a business process, through the product design and development, business implementation, operation, and retirement of computerized systems that support the business process.
This approach emphasizes the importance of critical thinking to identify data flows and data integrity as a critical aspect of product quality. It also involves the use of quality risk management principles to mitigate risks and protect patient safety and product quality.
Quality Culture
The classical Quality Culture
Quality Culture in the standard ISO 10010 is an environment in which employees share values, beliefs, history, ethics, attitudes, and observed behaviors supporting the achievement of a quality policy, objectives, and the delivery of products and services that meet the needs and expectations of customers and other relevant interested parties.
Wow, look at this definition! It explains exactly what quality culture is from a classical perspective.
Quality culture determines the way an organization works, impacts operational performance, and affects quality excellence, ensuring and exceeding customers' and patients' expectations and needs.
However, the concept of quality culture goes beyond following procedures, checking boxes, clearing audits, or displaying quality slogans.
It’s about cultivating a collective mindset, shared at every level of the organization.
Despite the absence of specific regulations relating to quality culture in pharmaceuticals, it is viewed as a critical element of an effective Quality Management System (QMS).
Now, let’s see quality culture from a different perspective.
Quality Culture in Pharma 4.0
Quality Culture in Pharma 4.0 extends beyond the classical definition of quality culture. It involves the use of advanced technologies such as artificial intelligence (AI), Internet of Things (IoT), and Big Data Analytics to drive a culture of quality throughout the entire product lifecycle.
Compared to the traditional concept, quality culture in Pharma 4.0 is more dynamic and agile, more open to innovation because digital technologies enable greater connectivity, agility, transparency, and collaboration.
For example, digital technologies:
- Drive innovation by providing real-time data monitoring and analysis, allowing for predictive quality management and proactive decision-making.
- Enable the integration of quality systems with other operational functions, enabling data visibility and transparency, and promoting seamless team collaboration and continuous improvement.
- Embraces adaptability, fostering a culture of knowledge and self-learning.
Unfortunately, it is easy to overlook the need to be people-centric in Pharma 4.0, where data and technology play a major role. Organizations need to have a strong leadership vision and plan for implementing the changes.
New technologies and processes require a mindset transformation and new ways of working. Quality is therefore achieved by having a strong QMS, which requires a commitment from senior management.
A supportive organizational culture that prioritizes employee well-being and involvement is essential to the successful implementation of Pharma 4.0.
Changing this mindset of resistance is at the core of digital transformation.
- Benefits of Quality Culture in Pharma 4.0
Creating a culture centered around quality in Pharma 4.0 yields numerous benefits essential for sustained success:
Openness to innovation, new technologies, and business opportunities
Members are open to learning new skills, taking on new roles, and adapting to new circumstances.
Enhanced connectivity and transparency
Networking all data sources creates transparency that enables shared information and collaboration to make informed decisions.
Democratized organization
People-centric democratization replaces the hierarchical structure of the organization and departmental silos. Technology allows communities to experiment, share, and learn by interest and expertise.
Increased productivity
Fostering quality culture improves productivity, and minimizes variations. This is key to streamlining quality assurance processes, reducing delays, solving issues, and preparing products on time. When there are fewer variations, employees can work more efficiently and effectively, resulting in higher output levels and faster turnaround times. This reduces the need for rework and ensures consistent output.
Talent retention
Team members acquire new skills in technology, which enhances their professional development, career advancement, motivation, and job satisfaction. Digital technologies enable remote working and flexible scheduling options, which can also improve work-life balance, ultimately contributing to higher retention rates.
- Organizational Change Management (OCM) in Pharma 4.0
OCM is the process of managing and implementing organizational changes to align with the principles and technologies of Pharma 4.0. This includes the adoption of digital tools, AI, and flexible manufacturing to increase production efficiency, streamline work, provide better experience to employees, and improve product time-to-market.
However, there are some challenges along the way.
Employees may be hesitant to adapt to new technologies and processes if they are unfamiliar with them. Improvements usually face obstacles due to a lack of understanding or fear of job displacement. In addition, pharmaceutical organizations may face financial and logistical challenges when integrating technology.
Despite these obstacles, embracing OCM is crucial for organizations to remain competitive.
Therefore, how can we implement OCM?
A successful digital transformation process can only be implemented if team members are aligned with the change. This is the objective of OCM: ensuring a successful digital transition by aligning the organization's culture, processes, and systems with the new digital technologies and capabilities.
Here are the steps we consider most important for succeeding in OCM:
- Establish a strong business case for digital transformation:
- To begin with, do a detailed examination of the shortcomings in the present situation of operations, specify areas of weakness, and inefficiencies, and also identify improvements.
- Establish a clear mission, vision, values, and objectives:
- Clearly define a mission and vision for the digital initiative that will correspond with the corporation's entire strategic objectives. Communicate the values in place, including collaboration, teamwork, and continuous improvement. Create smart objectives to give direction jointly with employees to the transformation journey ensuring all the goals are conquered the same way.
- Conduct the Pharma 4.0 maturity assessment:
- Achieve an accepted understanding of readiness and level of digital maturity. A thorough assessment is essential. This involves assessing the organization's readiness and the organization’s maturity level. The assessment should examine conditions covering, but not limited to, the infrastructure of technology, organization, and quality culture.
- Develop a holistic approach with clear priorities for digital initiatives:
- Leveraging the feedback from the maturity assessment conducted, go on to identify the gaps and formulate a roadmap for the progression of digital maturity.
- Engage team members and other stakeholders to discuss how the digital transformation will benefit their existing ways of working and the organization's competitiveness. Give priority to those initiatives whose effect is relatively significant and what is more, focus on areas where the organization can achieve quick wins and long-term success.
- Start operational implementation of Pharma 4.0.
- Develop a change strategy that explains program outcomes and benefits.
- Perform risk assessment based on current ICH Q9 and pharmaceutical principles.
- Improve processes.
- Empower team members.
- Create a Management Communication Strategy that outlines the desired outcomes and benefits. The plan should engage stakeholders and support the entire digital transformation.
- Create a global training and support strategy that ensures team members are equipped to handle new technologies and methodologies. Create an internal Community for knowledge sharing, collaboration, support, and guidance.
Key Human elements
Leadership in Pharma
Among all the key human elements of Pharma 4.0, leadership plays a pivotal role in developing a digitally matured organization.
Leaders need to direct and advise the current employees on new technological and procedural methods. One of the prerequisites for success is the necessity for them to have a common vision along with details on the implementation, as well as offer the required support for team members as they go through the stages of growing and adapting to the new roles and ways of working.
Leaders need to realize that digitalization is relevant to personnel and the structure of an organization, and must, therefore, go beyond old-school approaches.
Digital, people-centric environments need leaders to coordinate and develop teams, and adopt and implement new ideas that facilitate the constant improvement of the workflow.
Digital transformative leadership demands both technological competence, as well as management of changes placed within the system, allowing successful outcomes of the complexity.
Organizational model
With Pharma 4.0, organizations move from hierarchical structures to democratized structures that facilitate innovation, people empowerment, and seamless digital integration. The best organizational model is one that prioritizes collaboration, flexibility, and adaptability.
This is because:
- Pharma 4.0 requires organizations that are agile to regulatory requirements and technological advancements.
- Innovation helps organizations to leverage digital technologies to drive advancements throughout the product life cycle.
- The integration of digital technologies breaks down silos between departments and facilitates data sharing and collaboration.
- Customer-centricity facilitates needs identification and encourages innovation to meet requirements and needs to gain a competitive edge.
- People development ensures team members gain the necessary skills and competencies to leverage digital technologies efficiently.
Roles and Skills
The Pharma 4.0 initiative requires a variety of technical and non-technical roles. Their roles are crucial for the successful implementation and operation of digital technologies.
- Technical roles
Technical skills include managerial competencies and specific technical knowledge, such as data scientists, R&D, maintenance, engineering, automation, production, technical operation, quality, and IT. These skills are essential for the design, implementation, and maintenance of digital systems, as well as for the analysis and interpretation of data generated by these systems.
- Non-technical roles
Most non-technical roles are cross-functional and aim to eliminate barriers to knowledge and information sharing.
Note that It is possible to rightsize these roles in accordance with the size of the organization.
Organizational Culture
Organizational culture in Pharma 4.0 refers to the values, beliefs, norms, practices, and behaviors of the organization that promote collaboration, innovation, and implementation of digital transformation within a company to obtain high-quality, safe, and cost-efficient medicinal products.
It involves creating a culture where employees and decision-makers feel empowered to speak their minds, ask questions, and work together to achieve common goals in terms of digital and quality excellence.
This culture is critical in Pharma 4.0, where cross-department communication and collaboration are essential for the seamless integration of IT, manufacturing, and business functions.
A key element of the Pharma 4.0 culture is the importance of trust, delegation of responsibilities, and employee autonomy.
All members of the organization must have deep trust in each other and be willing to relinquish control. By empowering employees, companies can become more agile, adapt quickly to technological challenges, and find solutions more efficiently.
Creating a Pharma 4.0 culture involves a combination of top-down and bottom-up cultural approaches. In a top-down culture, senior executives drive the decisions behind culture, while in a bottom-up culture, employees have more say and opinion in what the culture looks
Tips and strategies to transform your organization’s culture
Transforming a pharmaceutical organization's culture to align with Pharma 4.0 principles involves comprehensive planning and strategic implementation. Here are some tips and strategies to facilitate this transformation:
Scilife view: Smart Quality
At Scilife, our approach to quality culture is far more than a mere regulatory box-ticking exercise.
As promoters of a proactive quality model, Smart Quality, we embrace digital technology as a spark that catalyzes value creation.
Through the use of technology for digital quality processes -eQMS, paperless workflows, cloud-based software, and new technologies like artificial intelligence - team members are empowered to take quality into their own hands and foster cross-functional collaboration.
Through active participation in quality initiatives, taking ownership of quality processes, and being transparent, employees encourage open communication between teams, which results in improved processes and outcomes.
Additionally, the use of technology allows teams to track progress in real-time, enabling them to quickly identify and address any issues promptly.
Therefore, we envision quality culture as the environment that uses technology at its full potential, empowering everyone in the organization to take ownership of quality, and engaging employees to make their own decisions based on real-time information provided by technology.
Technology is the seed for sustained quality excellence.
Conclusion
In Pharma 4.0, quality culture is a transformation approach driven by cutting-edge technologies that present many opportunities for innovation, agility, flexibility, and collaboration throughout the organization.
An organization can maintain a high level of sustained success in quality excellence and become customer-centric by applying digital tools and cultivating an atmosphere of openness and empowerment.
Technological advancements are driving the cultural evolution towards proactive quality management in the era of Pharma 4.0, which enables organizations to act fast, make the right decisions, and increase their long-term sustainability.