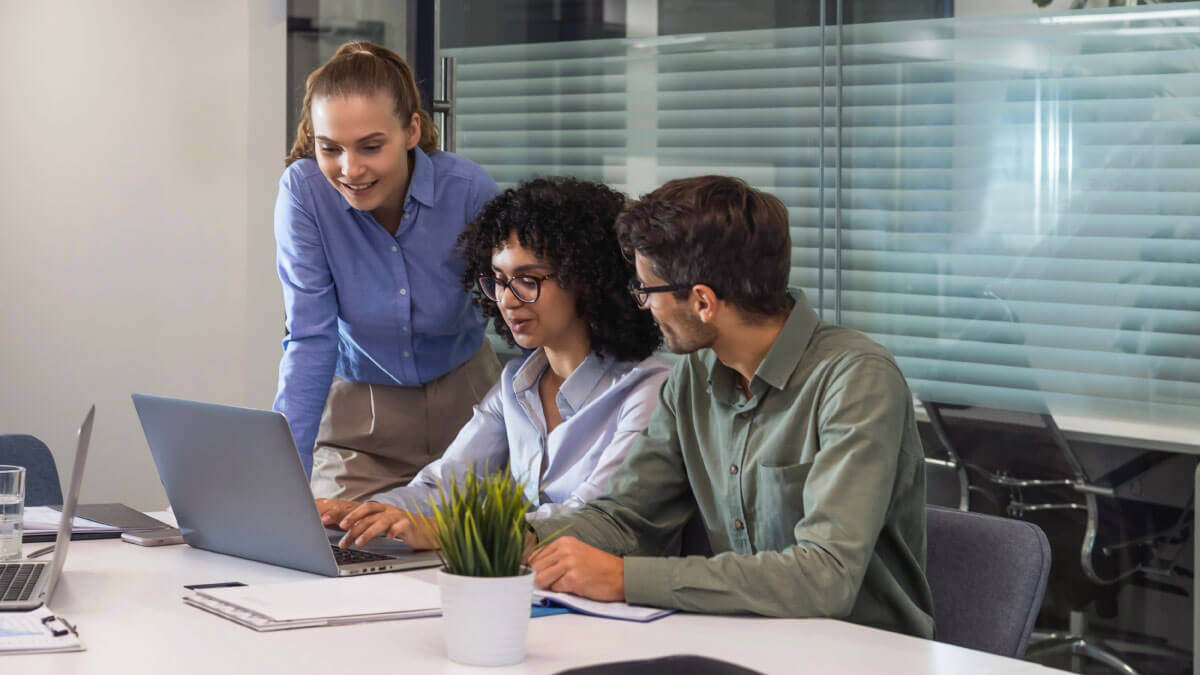
In the fast-paced and highly regulated life sciences sector, maintaining an effective Quality Management System (QMS) is critical to ensuring product quality, compliance, and continuous improvement.
But how do you achieve and sustain QMS effectiveness? You conduct robust Quality Management Reviews (QMRs), of course!
Not sure how? We got you!
This article explores the importance of QMRs, why you should do them, and what they entail. We also give you our best Scilife tips for how to improve your QMRs for optimal impact!
What is a Quality Management Review (QMR)?
A Quality Management Review (QMR) is a systematic evaluation of a life sciences organization’s QMS, conducted by senior management.
The primary objective of a QMR is to assess the performance of the Quality Management System (QMS), identify areas for improvement, and ensure alignment with organizational goals and regulatory requirements such as ISO 9001 Quality Management Systems.
QMRs are a cornerstone of decision-making in management review meetings, providing actionable insights for enhancing quality system effectiveness. By focusing on data-driven evaluations, QMRs help organizations identify trends, address risks, and prioritize continuous improvement initiatives within the organization.
Here are the key regulations that include Quality Management Reviews:
ISO 9001
In ISO 9001, Chapter 9.3 outlines the management review process. It emphasizes the need for top management to review the quality system at planned intervals to ensure it remains suitable, adequate, and effective.
This review should include a focus on past actions, external and internal changes, and quality system performance (e.g., customer satisfaction, quality objectives, nonconformities, CAPA). The review should result in identifying opportunities for improvement and potential changes to the quality management system, along with discussions about resources needed for quality management or projects.
ISO 13485:2016
ISO 13485 (Chapter 5.6) also focuses on the management review, similar to ISO 9001, but tailored for medical devices and in vitro diagnostics.
While the wording is different, the point is essentially the same as the ISO 9001 standard. The input remains the same but here there is a special focus on product quality and safety, which are critical in the medical device industry. As with ISO 9001, the output should lead to identifying areas for improvement and assessing resource needs.
MDSAP (Medical Device Single Audit Program)
MDSAP is a certification program aimed at harmonizing audit requirements across multiple countries. It ensures that medical device and in vitro diagnostic manufacturers meet specific regulatory requirements in five countries: Australia, Canada, the U.S., Brazil, and Japan.
An interesting aspect of this certification is the "Audit Approach" document, which describes the tasks an auditor should cover to ensure the company meets certification standards. Here are some key facts that are useful to know:
- Chapter 1 of this document addresses management review procedures, requiring that they be conducted at planned intervals.
- The review must cover the effectiveness of the quality management system, including quality objectives and quality policy.
- The document provides links to the specific regulations where these topics are covered, demonstrating how this requirement aligns with regulations in different countries.
ICH Q10
In the pharmaceutical sector, the ICH Q10 guideline highlights the importance of a management review of the pharmaceutical quality system.
This review should assess the achievement of quality objectives and evaluate system performance, including areas such as complaints, deviations, and CAPA. GMP guidelines also emphasize the need for a quality management system, reinforcing the importance of regular reviews to ensure ongoing quality compliance in pharmaceutical operations.
What is the most important objective of a Quality Management Review?
According to Didier Giffroy, Head of Quality & Regulatory Affairs at DiaSource ImmunoAssays, who led a Scilife training webinar on turning QMRs into drivers of lasting improvement, there isn’t a single answer—it depends on the quality maturity of your organization.
For companies just starting with certification standards, the main goal of the QMR is simply to meet the requirements of the standard. As the quality management system matures, the QMR evolves to provide greater visibility into quality processes within the organization.
Once quality is fully integrated into the organization, the QMR becomes a key source for identifying and implementing quality improvement solutions. In short, the objectives of a QMR will shift as your organization grows and matures.
What should be included in a Quality Management Review?
To maximize its value, a QMR should include the following key elements:
Supporting documents
The review process should be supported by relevant documentation, which may include:
- Internal and external audit reports
- Non-conformance reports and corrective action plans
- Customer feedback and complaint records
- Risk assessment documents
- Previous QMR meeting minutes
- Quality objectives and KPIs data
- Training records and resource allocation reports
Review inputs
Inputs for the QMR should be carefully curated to provide a comprehensive overview of the QMS.
These inputs typically include:
- Performance metrics: Data on quality objectives, customer satisfaction, and KPIs.
- Audit results: Findings from internal and external audits, including any identified gaps.
- Non-conformances: Trends and root cause analyses of deviations and corrective actions.
- Regulatory compliance: Status of compliance with ISO 9001 and other relevant standards.
- Changes affecting the QMS: Updates on organizational changes, regulatory updates, or new processes.
- Feedback from stakeholders: Input from employees, customers, and regulatory bodies.
- Resource needs: Assessment of current resources and additional requirements.
Review outputs
The outcomes of a QMR should drive meaningful actions and improvements. Key outputs include:
- Decisions and actions: Specific decisions to address identified gaps and improve the QMS.
- Updated objectives: Revisions to quality objectives based on current performance.
- Resource allocations: Adjustments to staffing, training, or technological investments.
- Risk management updates: New or modified risk mitigation strategies.
- Continuous improvement initiatives: Defined projects or activities aimed at enhancing quality and compliance.
- Documented minutes: Comprehensive records of the meeting, including action items and deadlines.
A structured agenda covering these elements ensures the QMR is both comprehensive and actionable, making it one of the most important aspects of your QMR.
Quality indicators to consider for your Quality Management Review
PI vs KPI
Performance Indicators (PI) and Metrics:
- Performance Indicators (PI) and metrics are similar in that they both measure the performance of a team or process.
- These are more focused on operational and tactical levels, typically used by teams on a smaller, more frequent basis to monitor how the team is performing and identify any issues within the process.
Key Performance Indicators (KPI):
- KPIs, on the other hand, are tied to the company’s strategic objectives and goals. They provide an overview of the company’s overall performance and should be the primary focus in Quality Management Reviews (QMRs).
- While performance indicators and metrics are discussed within teams, KPIs are the main indicators that drive strategic decisions and are discussed at a higher, organizational level.
Lagging KPIs vs Leading KPIs
Lagging KPIs:
-
Provide information about past performance.
-
Reflect what has already happened, essentially offering a status update.
-
Example: Number of nonconformities reported in a month, which tells you the historical data but doesn’t guide future actions.
-
Used to evaluate overall performance and review past outcomes.
Leading KPIs:
-
Focus on future actions and their potential impact.
-
Help predict what might happen based on current data or behaviors, allowing for proactive decisions.
-
Example: The number of nonconformities that are overdue or not yet closed. This allows the team to take corrective action before the situation worsens.
- Easier to define actions that can directly influence future results.
These are both important for your Quality Management Review because:
-
Lagging KPIs give you the status of past performance, helping you evaluate what happened.
-
Leading KPIs enable quicker changes and improvements by tracking actions that can shape future outcomes.
So our best advice would be to combine them both!
Why are QMRs important for QMS effectiveness?
We’ve gone through the details of what the QMR is and why you should do it. But how do you do it most effectively? Here are 8 steps to help you make your QMR the best it can be!
1. Prepare a comprehensive agenda
A well-structured agenda sets the tone for an organized and productive review. Begin by outlining the key topics that need discussion, ensuring alignment with both ISO 9001 requirements and the organization’s strategic objectives.
Include critical aspects such as process performance, non-conformities, audit findings, customer feedback, and improvement opportunities.
Share the agenda with stakeholders well in advance, allowing them to prepare and contribute meaningfully. The agenda should clearly define the objectives of the review, key evaluation areas, and the desired outcomes.
This preparation, which may seem excessive to some, ensures that all participants are aligned and focused on the review’s purpose.
2. Leverage technology
Take advantage of modern digital tools and technologies to enhance the efficiency and effectiveness of your QMR.
A centralized electronic Quality Management System (QMS) platform can help streamline data collection, ensuring real-time insights into key metrics. Use visual dashboards, automated reporting, and analytics tools to present data clearly and concisely.
Collaborative tools, such as shared document platforms or communication software, can help ensure all stakeholders have access to the most up-to-date information.
These technologies not only save time but also enable data-driven decision-making during the review process.
3. Engage stakeholders
QMRs benefit greatly from diverse perspectives, so involving cross-functional teams is essential. Doing so ensures a holistic assessment of the Quality Management System, as participants from different departments bring unique insights into challenges and opportunities.
Engage key stakeholders, including department heads, quality assurance leads, compliance officers, and operational managers, to foster a collaborative environment. Their input helps paint a complete picture of organizational performance and promotes shared accountability for implementing improvements.
4. Focus on actionable outcomes
The goal of a QMR is to drive meaningful improvements. To achieve this, focus on documenting actionable decisions and assigning responsibilities for follow-up tasks.
Use SMART criteria—Specific, Measurable, Achievable, Relevant, and Time-bound—to define clear and realistic goals.
Ensure that each action item is assigned to a specific owner with a clear deadline.
Tracking progress on these actions is essential to ensure they are completed, helping the organization continually enhance its processes and systems.
5. Incorporate risk-based thinking
Proactive risk management is a cornerstone of effective quality management.
During the QMR, dedicate time to identifying potential risks and discussing mitigation strategies. Review trends in areas like process failures, customer complaints, or market shifts, and use this information to adapt your risk management approach.
Incorporating risk-based thinking ensures that your QMS remains resilient, helping the organization anticipate and address challenges before they escalate.
6. Encourage open communication
A transparent and open communication environment is crucial for the success of a QMR.
Create a safe space where participants feel comfortable sharing their insights, concerns, and suggestions. This approach encourages honest discussions about challenges and fosters collaborative problem-solving.
By prioritizing open communication, organizations can uncover underlying issues that might otherwise go unnoticed and address them effectively.
7. Review regularly
Consistency is key to maintaining the momentum of quality management efforts.
Schedule QMRs at regular intervals—whether quarterly, biannually, or as needed—to stay ahead of potential issues.
Regular reviews provide opportunities to assess progress, address emerging challenges, and ensure the QMS adapts to changes in the regulatory landscape or operational environment. This routine review cycle helps the organization remain agile and aligned with its goals.
“Try to separate discussions on quality from business topics because, in my experience, once conversations shift to sales or revenue, they dominate the agenda, leaving only a few minutes for quality.”
Didier Giffroy, Head of Quality & Regulatory Affairs at DiaSource ImmunoAssays
8. Follow up effectively
A QMR is only as impactful as the actions that follow it.
After the review, ensure that all assigned tasks and decisions are tracked and completed within the specified timeframes. Use a centralized tracking system or project management tool to monitor the progress of follow-up actions.
Regular updates on these tasks ensure accountability and help maintain focus on continuous improvement.
By diligently following up, organizations can transform QMR findings into tangible results that enhance overall quality performance and drive sustained organizational success.
Quality Management Review best practices
Here are some best practices for conducting effective Quality Management Reviews (QMR) as recommended by Didier Giffroy, Head of Quality & Regulatory Affairs at DiaSource ImmunoAssays.
Give quality a vision
Ask yourself: Where do you want the quality system to be in five years? Then, use the QMR as a tool to align the organization with this quality vision and measure the progress that is being made towards those quality objectives.
Create a strategic quality path
You have your vision, and that’s great! But now you need to make it happen! This is where developing a clear strategy to achieve your quality vision comes in. Remember to link this strategy with key quality projects and a culture of continuous improvement that supports the overall vision.
Be pragmatic and action-oriented
You don’t have to make meetings long; what matters is that meaningful actions are taken. You can make them shorter and spend less time on preparation by not only the management and quality assurance teams but also those managing quality processes or owning quality projects. You should encourage these participants to prepare presentations, actively discuss topics, and contribute to action plans.
Use QMR as a control tower
Use the QMR to monitor the quality strategy and make corrections if needed to stay on track towards the vision. Allow for quick discussions and decisions to correct direction if necessary.
Support and reinforce quality culture
Give visibility to quality issues and projects within the QMR to all relevant people in your organization. The key is to get as many people as you can involved in quality discussions and continuous improvement efforts.
Frequency of Quality Management Reviews
Decide on a review frequency that fits your organization’s needs. While annual or semi-annual reviews are standard, consider quarterly or even more frequent reviews for dynamic, action-oriented discussions. The frequency should also depend on the maturity of the organization’s quality system.
Tailor topics to frequency
No need to get overwhelmed; Not all topics need to be covered in every QMR. Some topics can be presented only once or twice a year, depending on their relevance and progress throughout the year. That’s for you to decide.
Conclusion
Quality Management Reviews are a vital tool for enhancing the effectiveness of a QMS.
By providing a structured approach to evaluating and improving quality systems, QMRs empower life sciences organizations to maintain compliance, drive continuous improvement, and achieve their strategic objectives.
Implementing the tips outlined in this article will help you maximize the impact of your QMRs, ensuring sustained excellence in your quality management practices.