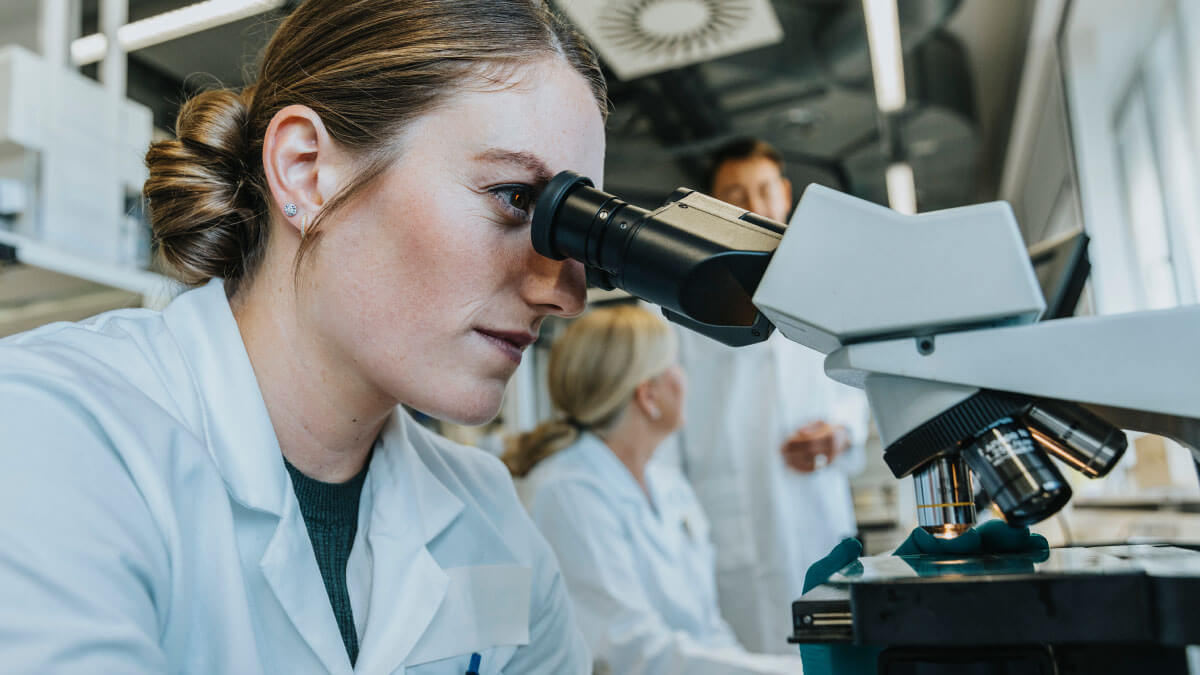
Regulatory agencies demand life science companies to produce high-quality, affordable medicines without compromising quality in manufacturing. For this reason, well-defined quality assurance goals are key for making life science businesses successful. If your company is also struggling with the challenge of balancing expenses Vs quality, then now is the time to redefine your company’s ordinary goals as Smart goals for quality improvement. There are several approaches with which you can make this happen. We will explore a few strategies in this article.
The Bold Vision Statement for Quality Goals
For a successful quality improvement program, it is essential to have your employees aligned with your vision. But, how can you expect your employees to align with your vision unless you publicize a bold vision statement that aligns with your quality goals? The vision statement of a company guides the employees in their day-to-day work. Therefore, ensuring that your quality goals are included in the vision statement helps your employees to be aligned with your quality improvement program.
For example, Medtronic has a mission statement that states that the purpose of the company is, “To strive without reserve for the greatest possible reliability and quality in our products; to be the unsurpassed standard of comparison and to be recognized as a company of dedication, honesty, integrity, and service.”
Similarly, Sandoz’s website mentions its purpose and ambition: “Sandoz contributes to society’s ability to support growing healthcare needs by pioneering novel approaches to help people around the world access high-quality medicine.”
The SMART Quality Goals
Another strategy for quality improvement is to define SMART quality goals, where S stands for Specific, M for Measurable, A for Achievable or Attainable, R for Relevant, and T for Time-bound. The following are some practical tips to define SMART Quality Goals for your company:
1. Making the quality goal specific
When dealing with the life science business, and especially the pharmaceutical industry there are some inevitable aspects you must not skip while defining the goals, and they are as follows:
-
-
Product Specific
-
Depending on the scale of your business you may have multiple products to monitor the quality. Every product needs to be monitored for different Quality Target Product Profile (QTPP) and Critical Quality Attributes (CQAs). At the same time, each product has different Critical Material Attributes (CMAs), and Critical Process Parameters (CPPs). Therefore, defining product-specific goals linked to the various QbD elements makes sense for quality assurance.
-
-
Complaint/Incident Specific
-
Although every manufacturer tries to deliver the best product quality, there are always some notorious products or processes that result in repeated complaints, or Out of Specification/Out of Target incidents. According to a survey conducted by McKinsey & Company, for most quality teams, the average investigation and closure cycle time hovers around 60 days—a few adverse events are reported late every month, and negative trends are addressed two or more months after the signals come in. It can take quality assurance teams even longer to identify complaints that collectively point to negative trends for a particular product or device. At the same time, less than 5 percent of incoming complaints are truly new events that have never been seen before. The remainder of complaints can usually be categorized into well-known issues, within expected limits; or previously investigated issues, in which root causes have been identified and were already addressed. Therefore, companies can save their time and resources by making the quality goals even more specific to such well-known issues in products and processes.
2. Making quality goals measurable
If you define specific quality goals as stated above you can easily set measurable targets for yourself. For example, you already know the range of analytical test results needed to meet your QTPP or CQAs specific to your product, therefore you can easily put a number to it in the form of product specification, and your quality goal can be based on product defects because of failing to meet the specification. You can calculate the possible number of defects out of one million opportunities.
The methodology of measuring quality in these terms is popularly known as Defects per Million Opportunities (DPMO) in the Six Sigma Philosophy. When you define a quality goal in terms of DPMO, it will always be defined in terms of reducing the number of defects from the current state.
For example, your measurable product-specific quality goals can be, “Reducing DPMO for product XYZ from 10 to 3.4”. Defining a measurable complaint-specific goal is even easier. It is also possible to just record the number of events in the past financial year and set a target for the upcoming financial year. Similarly, your measurable complaint-specific goal can be, “Reducing chipping complaints for product ZYX tablets from 100 to 10 in FY 2023-2024”. You can also set quarterly, monthly, or weekly goals based on their attainability.
3. Making quality goals attainable/achievable
It is always easier said than done. Therefore, while setting up these ambitious specific, and measurable quality goals, it is a good idea to cross-check the achievability/attainability of the goals.
For example, in the above case of ZYX tablets with chipping complaints, setting up a goal as “Reducing chipping complaints for product ZYX tablets from 100 to 10 in one week” would be unrealistic.
While it is important to utilize time and resources efficiently, it is equally important to set realistic goals. Therefore, always study the availability of resources, scientific limitations, or rate-limiting steps in getting things done while setting your quality goals.
4. Making quality goals relevant
Although you might be 100% sure that your quality goals are absolutely relevant to your company's progress, your employees may still feel they are not relevant to them as they are not linked with their deliverables and performance assessments. Therefore, it is extremely important to assign each goal to responsible team members and link it with their deliverables and performance indicators. You will need smart Quality tools described later in the present article to get it done effectively and efficiently.
5. Making quality goals time-bound
There are three primary reasons for making a quality goal time-bound as follows:
-
- Reason 1: A time frame is essential for defining measurable goals as stated above in the section titled “Making quality goals measurable”.
- Reason 2: The timelines are also essential for evaluating employee performance when the quality goal is made more relevant for an employee as stated in the section titled “Making quality goals relevant”.
- Reason 3: Another important reason for making the quality goal time-bound is to create a sense of urgency. If there is no time limit, it will never come on the urgent and important task list of the relevant team members.
All in all, it is important to make your quality goals time-bound.
Smart Quality Goals
SMART quality goals will give you a clear picture of what you need to do. Next comes the tricky part of how you will get it done. You will need a dedicated resource to keep track of progress on each quality goal. A more effective and efficient way of doing it is deploying an organization-wide Smart Quality tool that will help you do it digitally. The advantage of deploying such a Smart Quality tool is that:
- You can get a bird’s eye view with a dashboard to track the real-time progress of each goal.
- You can easily link quality goals with the key performance indicators (KPIs) of each employee and can create greater awareness about the quality program across the organization.
- Employees can actively participate by posting regular progress updates or creating their own quality goals.
- You will save time and resources.
- You will make more informed and data-driven decisions.
At Scilife, we can support you in meeting your goals with the help of our Smart Quality Software for life sciences.
Conclusion
In conclusion, setting SMART goals is a critical step for quality improvement in the pharmaceutical industry. SMART goals provide a clear and specific direction for the improvement process, which helps in reducing ambiguity and increasing the likelihood of success. By using the SMART framework, pharmaceutical companies can develop goals that are specific, measurable, achievable, relevant and time-bound. This framework ensures that goals are aligned with the overall business strategy, and they are realistic and achievable.
Moreover, the use of SMART goals can also help pharmaceutical companies to track progress and evaluate the success of quality improvement initiatives. By measuring the results of these initiatives, companies can identify areas for further improvement and refine their approach to achieve better results.
In summary, the SMART goal-setting enabled by Smart Quality Software is an effective and efficient tool for quality improvement in the pharmaceutical industry. It provides a structured approach to defining, tracking, and achieving goals that align with the overall business strategy. As the pharmaceutical industry continues to evolve, companies that embrace this framework will be well-positioned to succeed in a highly competitive marketplace.
Discover how a Smart QMS for Pharma can help you set and achieve your Smart goals.