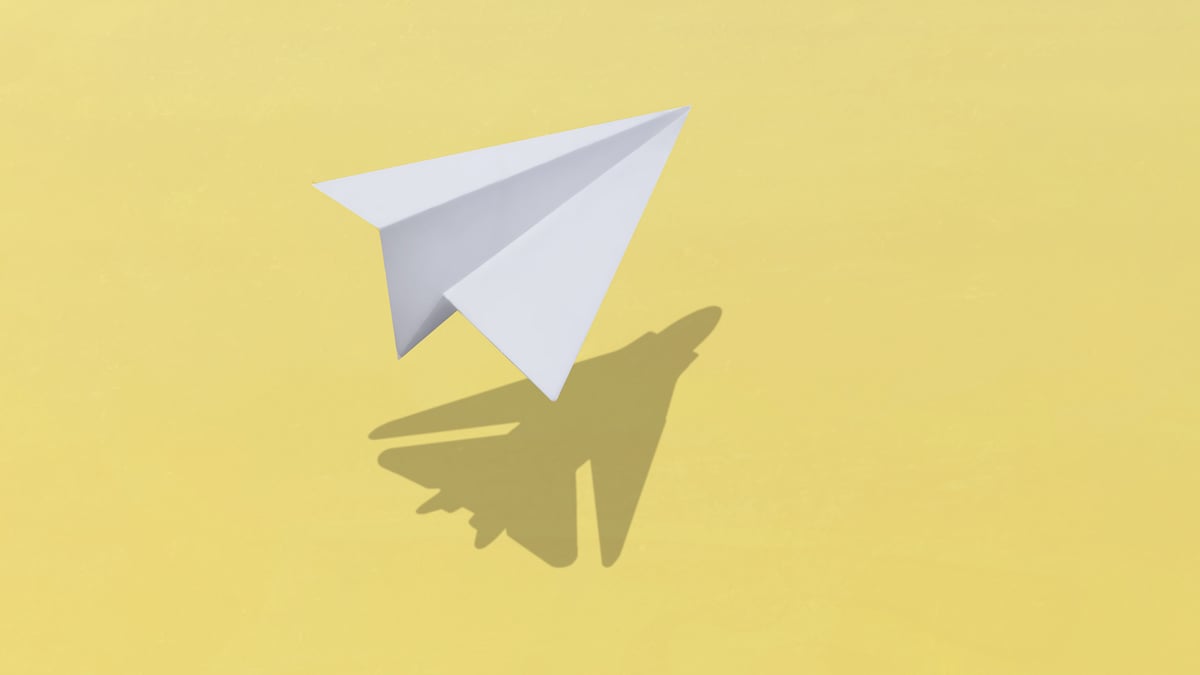
What is DMAIC?
DMAIC is an acronym for Define, Measure, Analyze, Improve and Control. The DMAIC process is the quality improvement methodology of Six Sigma that’s used for improving existing processes. It is an integral part of a Six Sigma approach, but in general, the DMAIC process can be implemented as a standalone quality improvement procedure or as part of other process improvement initiatives such as Six Sigma.
When and where to use DMAIC
In order to establish when and where you can and should use a DMAIC process, you first need to identify when you need a structured method for problem-solving. This is an important step in the primary ‘Define’ phase and can have long-term effects on the success of your Six Sigma program.
DMAIC is generally used by a project team that is trying to improve an existing process.
DMAIC provides structure since each phase of the process contains tasks and tools that will lead the team to find an eventual solution. While a DMAIC process may be sequential, it is not strictly linear. The process encourages project teams to be able to take a step back in case more information is needed.
The DMAIC process:
Methodology and Phases
Normally, a DMAIC methodology study is used as a part of a larger Lean Six Sigma project to create ‘breakthroughs’ in the organization. Each project is assigned to a Six Sigma leader (Black or Green Belt) and a team of subject matter experts.
Once the project (Problem) is determined by management, a project team will be appointed. The first thing to do is to create a project charter which will be followed by the team throughout the project. This project charter includes the 5 phases of the DMAIC methodology. Your team will use specific tools to work through each DMAIC phase.
1. Define
The D in DMAIC, Define is the first phase of the Lean Six Sigma improvement process. During this phase, the project team drafts a Project Charter, plots a high-level map of the process and clarifies the needs of the process customers. By conducting Process Walks and talking to process participants they begin their journey of building their process knowledge. Before moving on to the Measure Phase, the team refines their project focus and ensures they’re aligned with the goals of organizational leadership.
Tools used in the Define Phase
- Tools used in defining the problem and goal
- Project Charter
Effectively describes a process improvement project for both the team as well as leadership. Teams use the charter to detail the process issue at hand, the reason for addressing it, and what resolution the team should achieve. It’s also used to lay out what’s not being addressed. As the project unfolds, the Project Charter will be periodically reviewed and fine-tuned. A Project Charter consists of:
- Project Charter
-
-
- Problem statement
- Goal Statement
- Timeline
- Scope
- Members of the project team
- Business Case
- Tools used to define the process
- With SIPOC
In process improvement, SIPOC is a tool that summarizes the inputs and outputs of one or more processes in table form. It is used to define a business process from beginning to end before work begins. The acronym SIPOC stands for suppliers, inputs, process, outputs, and customers which form the columns of the table. SIPOC is used to define the process by developing a high-level map.
- Value Stream Map
An alternative tool to define the process by developing a high-level map. It’s more closely aligned with cycle time reduction projects. - Gemba Walk - also known as a Process Walk.
The team conducts interviews to collect data from the process to take a full picture of the process that’s in place. - Swimlane Map - to represent departments by using lanes.
Also, simple flow charts can be used to define the process.
-
- Tools used to define the customer and their requirements
- Voice of the Customer (VOC) Tools
(Including Surveys, focus groups, letters, comment cards, etc.).
VOC tools are used to understand feedback from current and future customers indicating offerings that satisfied, delighted or dissatisfied them. The team can establish the underlying issues in order to develop and implement measurable customer requirements. - Tree Diagram
This tool is used to create a tree chart from general to specific measurable requirements.
- Voice of the Customer (VOC) Tools
- Tools that inform others about the project progress
- A3
This tool is a simple and clear way to inform stakeholders and sponsors so they will engage through the project. - Relationship Map
this visual mapping tool is used for listing and assessing the relationship of potential stakeholders. - Stakeholder Analysis
this tool lets you layout who has a vested interest in how a process performs.
- A3
2. Measure
The M in DMAIC, Measure is the second phase of the DMAIC methodology. The performance of the process needs to be measured by using appropriate tools. Measurement tools will provide key indicators of the process's health and clues to where process issues are happening. It is vital to collect the data from the process before defining measures and evaluating the current performance or the baseline of the process.
Tools used in the Measure Phase
- Tools to quantify baseline measures
the team establishes a baseline of the process which will be the standard.
- With a Data Collection Plan
- With a Data Collection Plan
- Tools to refine the process measures
- By using Operational Definitions
- Tools to collect Baseline Data
- With a Check sheet
- With a Check sheet
teams should update the charter after completing each phase of the DMAIC
Other tools you can also use: Measurement analysis, exploratory data analysis, descriptive statics, data mining, run charts, Pareto analysis.
3. Analyze
Analyze, the A in DMAIC, is the third phase. The root cause of the problem should emerge in this phase of DMAIC. The team should take time and analyze the possible root cause(s) of the problem. The most common mistake is to proceed to the next phase too quickly without finding or understanding the accurate root cause.
If the team didn’t take time to perform the necessary analysis or walk through the process enough to see the real cause, then the next phases/steps wouldn’t be appropriate.
The crux of this phase is to verify hypotheses before implementing solutions. Only then should the team move on to the Improve Phase!
Tools used in the Analyze Phase
- Tools to Examine the process
- Time analysis
- Value-Added Flow Analysis
- Value Stream Map
- Tools to Display the data graphically
- Run Chart
- Histogram
- Pareto chart
- Box Plot
- Time analysis
- Tools to perform a Root cause analysis (RCA) to uncover causes
- Fishbone Diagram
- Failure mode and effects analysis (FMEA)
- Tools to Verify the Root cause
- Root Cause Hypothesis
Project Charter
teams should update the charter after completing each phase of the DMAIC
Other tools you can also use: Tree diagram, Brainstorming, Process Behavior Chart (SPC), Process maps, design of experiments, enumerative statics (hypothesis tests).
4. Improve
Improve, the I in DMAIC, is the fourth phase. Once the team determines the root cause of the problem, they can implement plans to eliminate these root cause(s). The Improve Phase is the stage where the team finetunes their countermeasure ideas, begins process changes, puts into action solutions, and data to confirm a measurable improvement. An organized improvement effort can create effective, innovative changes that improve the baseline measure and, ultimately, better the customer experience.
The Improve phase covers project management, risk assessment, process simulation, design of experiments (DOE), robust design concepts (including Taguchi principles), and process optimization.
Tools used in the Improvement Phase
- Tools to gather the best ideas to resolve the problem
- Brainstorming
- Benchmarking
- Classic Lean Improvements
- Tools to Select the most practical solution for the problem
- Solution Selection Matrix
- Weighted Criteria Matrix
- Impact Effort Matrix
- Tools to Develop Maps of Processes based on different solutions
- To-Be Map
- Value Stream Map
- Swimlane Map
- Tools to Test and Refine the Best Solutions
- PDCA/PDSA - Plan Do Check Act
- FMEA - Failure modes and effects analysis
- Tools to Implement Best Solutions
- Pilot Checklist
- Implementation Plan
- Tools to Measure to Ensure Improvement
Other tools you can use: 5S, 7M tools, Work Cell Design, Setup Reduction, Kanbans, Project planning and management tools, prototype, and pilot studies.
5. Control
The Control Phase, the C in DMAIC, is the last phase of the DMAIC methodology. After all, improvements can only be sustained by controlling them. So, how do you control the improvements?
If the improvements in place solve the problem permanently, it means the project is completed effectively and the actions are taken effectively to improve the process permanently. To be able to say that confidently, a defined control method should be used after a defined period. The team should develop a Monitoring Plan to follow the success of the updated process, and create a Response Plan in case there is a dip in performance.
The control phase covers process control planning, using SPC for operational control, and PRE-control.
Tools used in the Control Phase
- Tools to Ensure the New Process Is Managed and Monitored
-
- Monitoring Plan
to document what is needed to keep an improved process at its current level. - Response Plan
in case there is a dip in performance.
- Monitoring Plan
- Tools to Document the improved process
- Documentation
- Standard Work
- Visual Management Checklist
- 5S
- Tools to Transfer the improvements
-
- Quick Wins
- Visual Boards
- Tools to Share and celebrate the team’s success
-
- Gallery Walks
Continuously Improve the Process
The last but most fundamental step of the control phase (cheering the team’s success!) doesn’t signify the end of improvement, it’s just a milestone and an important ‘resting point’ in the continuous improvement journey. Each successful improvement sparks the problem-solving culture in your company to grow. That’s why we like to think that the “C” in DMAIC stands for “Control” but also for “Continue”, and maybe for ‘Celebrate’! After all, celebrating team effort encourages even better performance in the future.
The point when a project is closed is a great moment to reflect on the four Lean principles—Value, Flow, Pull, and Perfection.
-
- Value:
Determine what steps are required (are of “Value”) to the customer - Flow:
Remove Waste in the system to optimize the process to achieve a smoother workflow - Pull:
Ensure the process answers customer demand (“Pull” = want) - Perfection:
Continuously aim for “Perfection” within the process
- Value:
Other tools you can use: ISO 900x, bid models, cost estimating models, reporting system.
To Sum it Up
DMAIC is a useful process to use for a structured approach to continuous improvement within your company. It can be used as an integral part of a Six Sigma approach but also as a standalone methodology. Just remember that these approaches are not replacements for your quality system, they’re merely frameworks that support robust and continuously improving quality management! There are many valuable tools available to successfully proceed through each DMAIC step, of which we’ve mentioned the most common ones. If you follow the DMAIC process rigorously you will not only see actionable results but undoubtedly foster a growing culture of improvement within your organization.
Get to know how Scilife Smart QMS can further help you on your journey to continuous improvement by streamlining all the processes within your quality management system and connecting workflows in fast, intuitive and efficient ways.