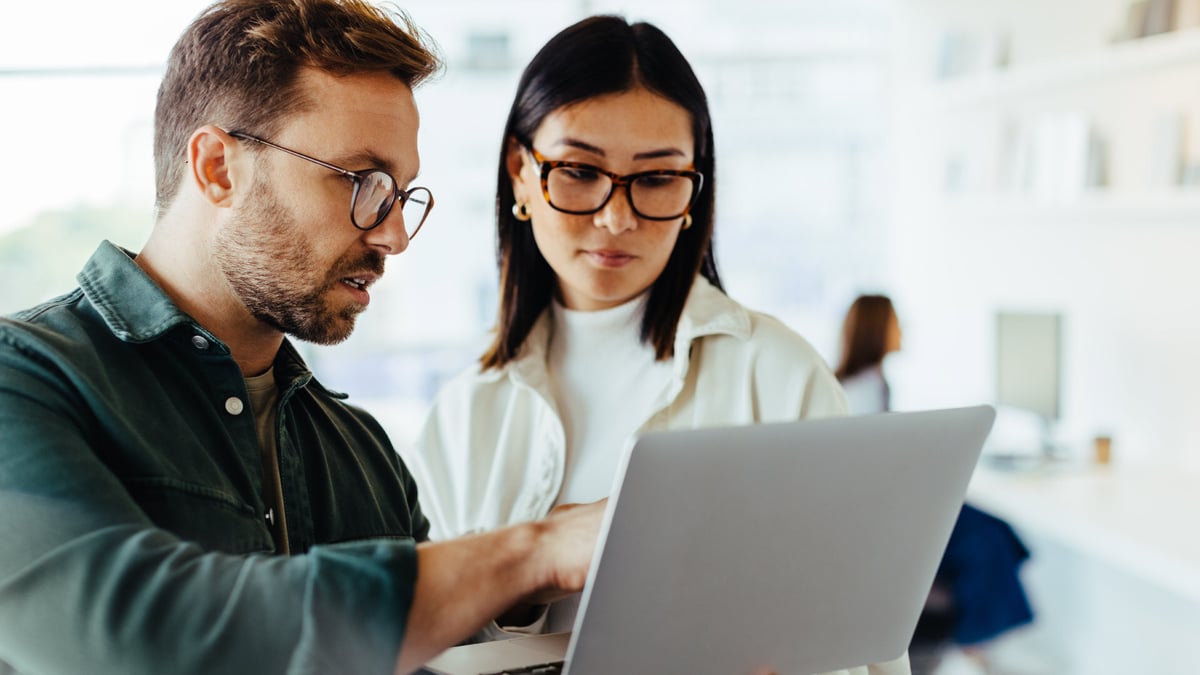
Quality management software is gaining traction as a dependable adjunct to quality management teams. The benefits are substantial, especially in life sciences, where quality translates to rapport and, subsequently, sales.
This growing reliance on quality management tools reflects a universal truth across industries: whether in services, merchandising, or manufacturing, quality is non-negotiable. As the market becomes more competitive, ensuring quality is seen as a must-have trait for every organization, regardless of the service or size.
Moreover, rigorous quality maintenance is especially vital in quality-sensitive and high-risk fields like the life sciences. Even minute risks pose considerable threats to public safety and patient health. That is why most organizations and life sciences professionals avoid risks and use products from companies they can trust to maintain state-of-the-art product quality.
However, maintaining quality is an extensive process. Larger operations need hundreds of hours of work and specialized teams for thorough quality assurance. Fortunately, with the help of advanced technology, the process can be cut short.
Companies implementing quality management software can gain a clear insight into product production, plan more effectively, target specific concerns, and gain opportunities for scaling and streamlining operations. In this article, we will explore how eQMS solutions for life sciences can drive operational excellence while ensuring regulatory compliance.
What is operational excellence in life sciences, and how does it help with business objectives?
Operational excellence is often used to describe business leaders in their sectors. The term refers to a work culture that focuses on continuous improvement. According to IBM, it is not just a culture but an approach to business. If implemented correctly, all organization members will focus on producing quality products and satisfying clients.
Operational excellence is based on the idea that quality begins at the source, and each member of an organization has influence over the final product. It is based on Dr. Shigeo Shingo’s principles.
Operational excellence is not a single method but an amalgamation of steps, such as seeking perfection, accountability, and thinking systematically. Shingo has ten guiding principles that create the core values for operational excellence.
How do Shingo’s principles help businesses boom?
Leading organizations use operational excellence methods to reach target KPIs. Any organizational, financial, or cultural goal can be achieved if approached with the right tools and techniques. For example, suppose a company wants faster production. In that case, by implementing operational excellence practices it can facilitate the identification and removal of roadblocks in the supply chain, product management, and manufacturing.
Operational excellence methods focus on achieving optimum workflow while not skipping details and solving problems from their roots. This approach to quality maintenance works perfectly for life science organizations.
The life science industry is often more quality-focused than others. An excellence-focused work culture promotes high efficacy, safety, and customer service. The process can be even more effective with quality management software. An integrated digital system ensures smooth collaboration, elimination of organizational delays, fast workflows, traceability, and accountability.
How can quality management software contribute to your operational excellence?
Operational excellence requires a fresh look at your operations, identifying where the problems are, and empowering your team to tackle them consistently and effectively. This is the base of an excellent quality management system. For this reason, according to IBM, one of the operational excellence tools is business and quality automation tools. Automating parts of the process, even the quality management process, takes the load off of human employees and still allows room to strive for continuous quality improvement.
An eQMS is the modern equivalent of an entire QMS team dedicated to documentation, resource management, audit management, risk management, corrective actions, etc.
If appropriately used, quality management software can be an excellent tool for driving operational excellence. Read on to learn how:
Main benefits of an eQMS for operational excellence
- Streamlined monitoring: Quickly identifies issues and enables prompt corrective actions.
- Simplified regulatory compliance: Automates documentation and ensures seamless adherence to standards.
- Enhanced risk management: Identifies potential risks and prevents adverse events.
- Data-driven decision-making: Provides actionable insights for better resource allocation and process improvement.
- Improved customer experience: Delivers safer products and fosters trust through quality and responsiveness.
Streamlined monitoring for operational excellence
eQMS is perfect for monitoring key metrics. An in-depth analysis of patterns, delays, and complaints derived from monitored data can then be used to pinpoint weak links or quality lapses in the production, supply, or manufacturing channel. While manual analysis can take days, properly designed eQMS software can point to the source of the issue in minutes. Following the detection, prompt corrective action (also digitally assisted) and preventive system implementation make way for sustained quality improvement, achieving operational excellence.
Simplifying regulatory compliance
Some quality management software has extensive document management features. This feature paves the way for a smooth regulatory compliance process. Regulatory authorities, like the FDA, ISO, and EMA, emphasize transparent and detailed reports regarding pharmaceutical products and medical devices development, clinical tests, performance and safety reports, risk management plans and reports, etc. Using an eQMS, these protocols and tests can be readied for submission as they are being done. Most eQMS also have built-in programs to automate the compilation of data and segment them according to use and source. Some even have features specifically for regulatory writing, such as literature review writing. All these features fortify the preference for perfection as part of operational excellence.
Enhancing risk management and audits
Monitoring data and processes used throughout the organization takes away much of the risks. Many eQMS act as an extension of the risk management system, finding roots of potential issues and preventing adverse events. Flagging processes and teams based on adverse event reports, tracing faulty products back to the source, and identifying potential risk sources are extremely useful in creating low-risk, high-impact medical products. Features for audit management; audit scheduling, auto task assignments, data analysis, and auto reports make regular internal audits impactful. It’s a great tool to track continuous quality improvement efforts.
Driving data-informed decision-making
One of the highly useful features of eQMS for businesses is data-based suggestions. As the system has access to all processes and their data regarding the product, comprehensive and multifactorial assessments can be done, allowing management to make informed decisions. Not to mention, it saves time and resources, encouraging precise and effective resource distribution. This is an invaluable tool in an organization inspired to have operational excellence. It is also a great tool for management to implement an excellence culture in the office, using data to demonstrate goals and challenges - helping your organization to become more data-driven.
Enhancing customer experience
Ultimately, all quality management efforts are there to improve the customer experience. Using QMS software, safer and more effective medical products are made, ensuring happy and loyal customers. In addition to quality, automated replies to customer feedback, feedback analysis, and AI chatbox features foster a trusting relationship. Adding the CAPA management features of QMS software solidifies its usability as the ultimate customer management slash operational excellence tool.
Recommended learning: Still not convinced an eQMS is what you need? Here are 8 reasons why you might be missing out.
Scilife tips
Quality management software is the latest tool in a quality manager’s arsenal. From document management to risk management to full-fledged CAPA tools, eQMS software comes with various features that allow organizations to prioritize quality and excellence.
This software has the unique ability to work with teams of experts, utilizing data and insight to optimize operations. Quality management software is the next big thing in regulation and quality assessment. eQMS is a great fit, especially for medium to large businesses looking to scale, reduce human error, keep a low-risk margin, and increase profit. It allows you keep control of things that need human interventions and automate the rest.
Our tip is to find the software that suits your organization. Before buying, consider what you need to achieve operational excellence. Investing in quality management software is a leap toward driving operational excellence that supports the organization’s vision and growth strategy.
Conclusion
At Scilife, we believe in sustained growth and quality excellence. Our quality management software is designed to be your partner in steady growth and long-term success, providing a competitive edge in the ever-competitive life science industry.
Scilife Smart QMS is proactive rather than reactive. We bring innovation and value to quality management and create tangible changes in our partnering organizations. Our philosophy is elevating quality beyond simple compliance through Smart Quality. Through a quality-conscious culture, we seek to reduce costs and implement sustained operational excellence.