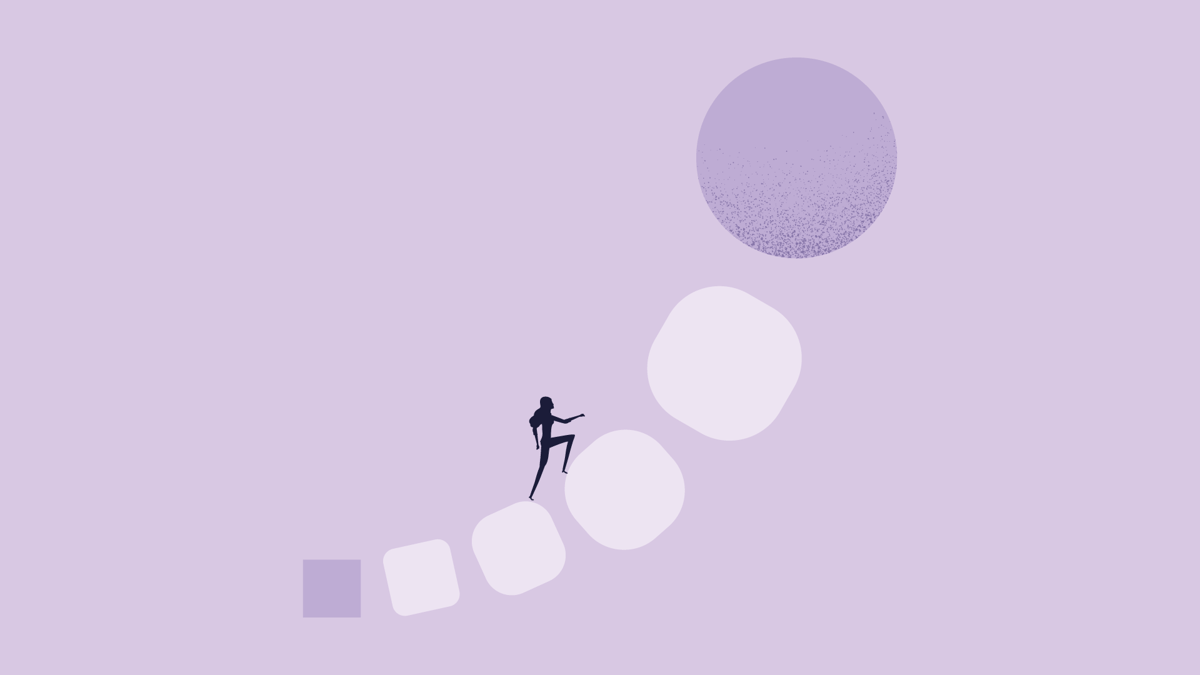
Lean Thinking is centered around building efficient manufacturing operations by defining value from the customer's viewpoint and continually improving how value is delivered by eliminating wasteful resources or resources that do not contribute to the value goal. In short, lean promotes preserving value with less work, with the ultimate goal of providing excellent value to the customer through a process that has zero waste.
Pioneers of Lean Thinking
Toyota Production System pioneered Lean Thinking in the middle of the 20th century. Taiichi Ohno is considered one of the founding fathers of lean manufacturing. He dedicated his career to establishing solid and efficient work processes based on Lean Thinking.
Lean Thinking for Life Science Industries
Historically, companies in the life science industry dealt with big budgets, large-scale operations, and many regulatory compliances. It was a sector in which the players could enjoy high-profit margins. However, the situation has shifted in recent years due to cut-throat competition, a changing patent landscape, and price control acts applicable in various geographies. This evolution catalyzed the application of Lean Thinking in the life science industry.
Challenges for Lean Thinking in the Life Science Industry
Unfortunately, years of high margins and large budgets caused a less cost-conscious culture in the life science industry, a source of challenges in implementing Lean Thinking strategies. Another challenge is pharma's fiercely independent business functions, divisions, and geographic units. The ‘silo’ mentality remains deeply entrenched at most drug companies. This approach is contrary to Lean culture which is all about teams, process thinking, and cross-functional collaboration. What's more, Lean transformation in the life science sector is still a relatively new concept. Nevertheless, life science companies are taking note of the extraordinary success of Lean in the automotive industry, and following suit.
Lean Wastes (Mudas)
Engaging in wasteful activities (known as Mudas) can be a major roadblock that negatively influences a company's work processes. For example, in the context of manufacturing operations in life science industries, the following activities can be considered wasteful:
- Transportation
In manufacturing, it may mean moving parts and materials from one place to another. - Inventory
Undelivered products. Overstocking with equipment that is not flexible (concerning utility and batch size), is specific to a product, or doesn't have immediate use. - Motion
Unnecessary movement of employees, materials, and machinery. - Waiting
An intermediate product is waiting for the subsequent stage of processing or finished products in waiting for customer delivery. - Overproduction
Producing more than required to fulfil customer demand. - Over-processing
Process steps that are unnecessary to meet product specifications. Adding a feature that doesn't bring value. - Defects
Unmet product specifications that require rework.
Therefore, the first step that life science companies need to take to implement Lean Thinking is workaround strategies to minimize these Mudas. To begin the transformation journey, companies can turn to various Lean Tools that seasoned Lean Practitioners have developed over the years.
Lean Tools
As stated above, eliminating all non-value-added activities is synonymous with lean and will continue to drive future sustainability for life science companies. Additionally, there are various Lean Tools that can make this step easy:
- Value Stream Mapping:
A visual tool that displays all critical steps in a specific process and quantifies the time and volume taken at each step to identify and minimize the "waste." - Heijunka:
A Lean method for reducing the unevenness in a production process and minimizing the chance of overburden. - Nemawashi:
This technique relates to building a consensus using a one-on-one discussion with each member of a decision-making group. It anticipates resistance and aligns the proposed change with other perspectives and priorities in the organization. - Total Productivity Maintenance:
This is a strategy based on the idea that everyone in a facility should participate in maintenance rather than just the maintenance team. - Poka-yoke:
This Japanese term means "mistake-proofing," and it refers to any tool or mechanism that avoids mistakes. - Just in Time:
An inventory management method in which goods are received from suppliers only when they are needed. - Single Minute Exchange of Die:
This technique relates to reducing changeover times to the "single" digits. The technique aims to convert a maximum number of changeover steps to "external" (performed while the equipment is running) and simplifies and streamlines the remaining steps. - 5whys:
This is a popular technique that involves iterative interrogation to explore the cause-and-effect relationships underlying a particular problem.
The choice of methodologies/tools to be implemented depends on various factors, including experience, value delivered, resources required, the number of people involved, the ability to create transformation, etc.
In the next couple of paragraphs, we explain how companies utilize Lean Thinking and lead by example.
Companies Leading by Example:
GlaxoSmithKline
GlaxoSmithKline Bio eliminated their wasteful activities related to motion by applying the concept of "one roof" development with inspiration from carmaker Renault. GlaxoSmithKline Bio used it for their vaccine business by centralizing development in one location. As a result, the company successfully cut down on waste. Also, it achieved a decision-making cycle time reduction, which resulted in the 18 months early launch of its HPV vaccine (Cervarix).
AstraZeneca
AstraZeneca successfully implemented Lean equipment purchasing and operating strategies. The company has been using the following big picture points:
-
- Use a small, cross-functional team of seven or fewer people.
- Including marketing and sales information, as well as future projections, in the project charter.
- Select equipment that's flexible.
- Specify how to purchase equipment and how to decide upon vendors.
- Develop a URS to present to original equipment manufacturers and negotiate aftermarket services.
- Understand that Lean packaging equipment purchasing and machinery operation involves reducing waste.
- Know those waste areas can include overproduction or production ahead of demand, which can cause waste in the form of expired products.
- Minimize motion waste during product transportation between the warehouse and the packaging line, in staging areas, and where the product is loaded into areas on packaging equipment.
- Use a small, cross-functional team of seven or fewer people.
How to implement Lean Thinking
in your organization
Excited to implement Lean Thinking in your organization? Here’s what you can do to get started. All you have to do is focus on these three critical strategies:
- Continuous Manufacturing:
End-to-end operations enable continuous material movement and no in-process storage/quarantine. Additionally, it offers complete visibility of all operations on the same floor. - Quality by Design (QbD) and Process Analytical Technology (PAT):
Inspection and QC are non-value-adding activities. Implementing QbD Principles and PAT tools helps avoid the stop-look-go approach and thereby minimizes the time taken for inspection and quality control activities. - Being Digital:
It saves huge sums on storage space, excess motion, and decision-making time. Digital transformation can be catalyzed by tools such as e-QMS, e-LNB, knowledge management, and project management software.
Use these three key strategies and you’ll cut down on manufacturing waste drastically.
Measuring the Lean Thinking Progress
After implementing Lean Thinking in your organization, the next important step is to keep measuring its performance. To be more precise, companies need to develop appropriate objectives, target values, and initiatives needed to achieve the target for the following four perspectives:
- Customer perspective
(factors that really matter for customers) - Internal Business Perspective
(processes that have the most significant impact on customer satisfaction) - Innovation & Learning Perspective
(ability to innovate & improve) - Financial Perspective
The performance measurement of the above four perspectives in meeting the desired target is an indirect measurement of Lean thinking progress.
Conclusion
In conclusion, Lean Thinking promotes simplified processes, high performance, and agility in the business climate, making companies better equipped to deliver in challenging circumstances.
It plays a pivotal role in continuous improvement through:
- Competing effectively in today's global economy.
- Balancing customer pressure for price reductions.
- Adapting immediately to fast-paced technological changes.
- Continued focus by the marketplace on Quality, Cost, and Delivery.
- Developing standardized processes to obtain uniform superior-quality outcomes.
Hence, life science companies should take their cue from the automotive industry and transform the future of the sector through Lean!