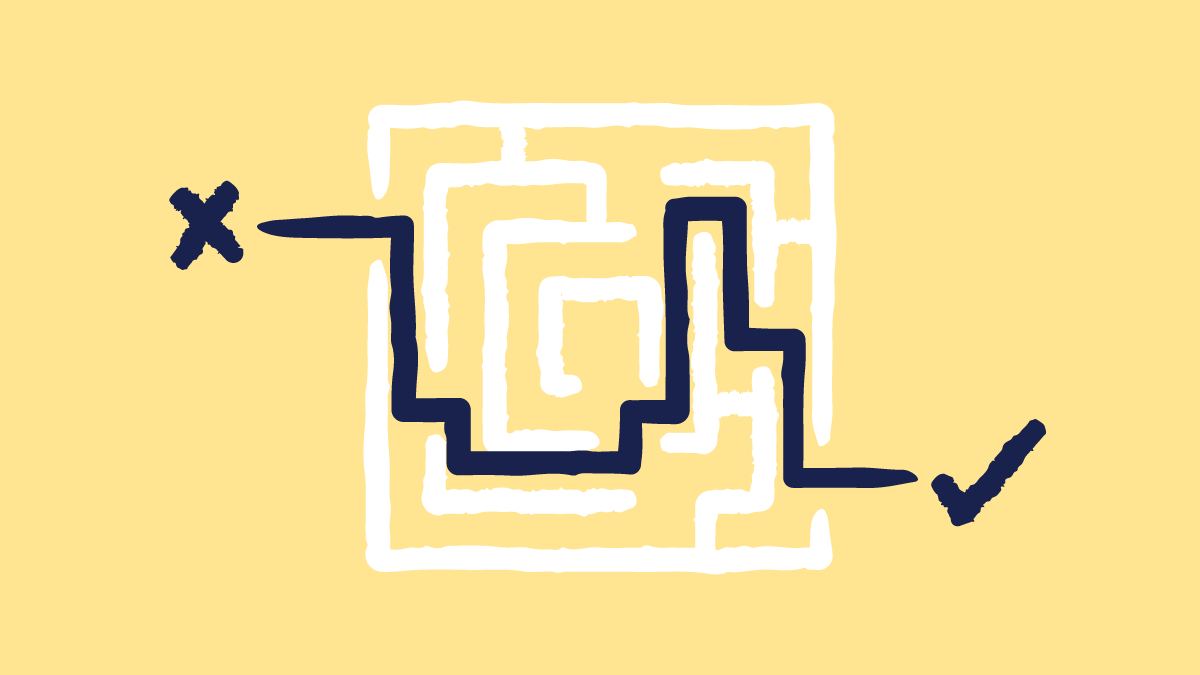
As one of the most regulated industries on the planet, the challenges in the pharma industry are countless, especially when it comes to managing a pharmaceutical Quality Management System.
A QMS in the pharmaceutical industry has many moving parts, requiring the collaboration of cross-functional teams, often across multiple sites, while ensuring strict compliance with global regulations. Some common pharmaceutical regulations include GMP, FDA 21 CFR Part 210 & 211, 21 CFR Part 11, and EU GMP Annex 11, among others. And as we all know, any compliance mishaps can lead to a spiral of consequences, from regulatory warnings to product recalls and reputational damage.
This is no easy task for quality professionals from the industry. Maintaining a strong QMS requires balancing complex processes, ensuring high-quality and accurate documentation, and implementing effective risk management strategies, all while keeping operations efficient.
In this article, we’ll explore the most common pharma QMS challenges and provide practical solutions to help your organization stay compliant, improve efficiency, and build a culture of continuous quality improvement.
What makes a good QMS in the pharmaceutical industry?
Before we get started, let’s explore what a good QMS should look like. Take a look at the diagram below, this is how your pharmaceutical QMS should function in an ideal world:
- Your audit results and management reviews feed into the QMS, enabling continuous improvement.
- You have established quality policies with clear quality objectives in place.
- Your Corrective and Preventive Actions (CAPAs) help you improve processes continuously, addressing any audit findings and mitigating risks.
- There is a constant and effective analysis of data: monitoring, measuring, analyzing, and improving processes to ensure sustained quality and hitting those quality KPIs.
Source: Unlocking the Power of Your QMS, John E. (Jack) West, Charles A. Cianfrani
However, the reality of implementing and maintaining a QMS is far from simple. While the ideal system we’ve described sounds effective, for many QA professionals, it often feels like walking against the wind on ice skates while carrying a bag of bricks on your back.
When critical elements are lacking or processes break down, organizations risk losing control, encountering compliance failures, and ultimately compromising patient safety.
Common QMS challenges in pharma
Data integrity and data management
The life sciences industry, including pharma, generates the equivalent of 5 billion pages of text every 24 hours—amounting to tens of terabytes of data every single day. As you can imagine, data storage becomes a major concern, as how you store your data impacts costs, security, and resource requirements in significant ways.
Then there’s accessibility, can you quickly pull the documents you need during an audit? If not, you're in trouble. The lack of data standardization also complicates things.
How can you analyze and use data effectively if it's inconsistent and scattered across different systems?
Compliance is another big factor. Is your data management in line with regulations like HIPAA? Is your data reliable, accurate, and trustworthy? Nowadays, regulators are increasingly focusing on data integrity to ensure patient safety.
Scilife Tip:
Developing a strong data governance framework, designating a data steward, implementing FAIR principles, and leveraging technologies like AI and ML to analyze large datasets, identify patterns, and predict future trends can help you mitigate some of these challenges.
Of course, using life sciences data management software like Scilife, tailored specifically for the pharmaceutical industry with built-in digital audit trails, should be at the core of your strategy.
CAPA and risk management
CAPA failures have been identified as one of the most common audit issues in the pharmaceutical industry in recent years. Inadequate root cause investigations, poor analysis of deviations, product failures, and customer or patient complaints, along with insufficient CAPA systems, have all contributed to these challenges.
On the other hand, reactive instead of proactive risk management is common in many pharmaceutical companies as they struggle to continuously monitor outcomes and predict risks.
Scilife Tip:
To address these challenges, focus on building a robust CAPA management system from the start. Use a centralized, digitized system, review it regularly, and ensure it stays current and effective. Establish clear communication guidelines, and make sure each CAPA is reviewed thoroughly with a cross-functional team involved in the process.
While deviations and nonconformities are inevitable, detecting them early is crucial for preventing quality issues and driving improvement. What’s the ultimate goal? Prevent these issues in the first place and you can do that through effective risk-based thinking and risk management strategies.
Quality culture
Resistance to change, lack of manager buy-in, a blame culture, and quality being seen as just the quality department’s job, sound familiar? These are all signs of a weak quality culture. Every quality assurance manager dreams of a strong, organization-wide quality culture, but sadly, that’s often not the reality.
Building that quality culture is a mindset shift, it requires changing the attitudes of employees used to the status quo, strong support from leadership, and decisive action. This is something that cannot be achieved overnight and is a constant struggle for quality teams as they know their QMS would be so much better if only everybody else was on board.
Scilife Tip:
Start by assessing your quality maturity with our test. ISPE’s framework for cultural excellence is built on six key dimensions that drive operational greatness:
Building leadership and vision
Challenging mindsets and attitudes
Active engagement through Gemba walks
Leading quality indicators and monitoring key triggers
Transparent oversight and review
Implementing cultural enablers (e.g., learning organizations, proactive problem-solving, and recognizing organizational change).
Continuous improvement
Quality assurance professionals are often pulled into handling immediate issues; product defects, audits, compliance concerns, or customer complaints. This reactive focus leaves little room for proactive improvement efforts, especially when day-to-day operations and regulatory compliance take priority.
At the end of the day, continuous quality improvement is about teamwork. In organizations with fragmented departments or poor communication, QA managers often struggle to align cross-functional teams around improvement initiatives, making progress slow and difficult.
Scilife Tip:
Here at Scilife, we recommend driving continuous improvement in your organization by adopting one of the tried-and-true methodologies. The most popular approaches are Lean Thinking, Six Sigma, and Kaizen. Let’s take a closer look at each:
Lean Thinking: A continuous transformation that streamlines operations by eliminating waste while maintaining or increasing value.
Six Sigma: A data-driven method that uses statistical analysis to detect and eliminate inefficiencies and defects, reducing process variation.
Kaizen: A philosophy of small, incremental improvements that, over time, lead to significant process enhancements.
Supply chain management and compliance
The pharmaceutical industry is one of the most heavily regulated fields worldwide with constantly evolving standards, making compliance across various regions of the supply chain extremely difficult. This means companies must stay on top of continuously updating their processes, documentation, and training programs.
To add to the complexity, the supply chain involves multiple suppliers and manufacturers, which generates gigantic quantities of data to manage and ensure visibility and traceability. And if that wasn’t enough, let’s not forget that the supply chain is vulnerable to disruptions like natural disasters, geopolitical tensions, pandemics, and supply shortages.
Scilife Tip:
One of the most effective ways to manage a supply chain is by implementing advanced technology solutions. For example, an eQMS can automate repetitive tasks and digitize records, significantly reducing manual errors and improving efficiency. Having suppliers, manufacturers, and distributors aligned on a digital platform also makes it easier to communicate and collaborate.
On the other hand, blockchain technology can further help you enhance traceability by providing a secure, immutable ledger that records every transaction, helping combat counterfeit drugs and ensuring transparency.
Siloed and hybrid quality management
As we all know, documentation is the lifeblood of quality management. When it’s managed in a fragmented way, some on paper, others in a mix of digital and paper formats, it leads to disconnected information streams across the organization.
This fragmentation makes it difficult to gain a comprehensive, real-time understanding of processes, making it extremely hard for the quality assurance team to spot potential issues early and react before they escalate. The consequences? Product quality and compliance are compromised, and collaboration becomes inefficient and frustrating.
Scilife Tip:
The best way to unify your documentation and data is by embracing modern technology, like an eQMS. It brings everything together in one secure place, making your processes more efficient and easier to manage.
One of the standout benefits of an eQMS is how it seamlessly integrates key QMS functions like document management, risk management, and CAPA, making data extraction for KPIs easy. With all your metrics in one spot, you can quickly spot weak areas, make better decisions, and ensure everyone stays aligned with real-time insights from anywhere.
Key takeaways
- Make data work for you, not against you. A strong data governance framework and digital tools will help you ensure integrity, compliance, accessibility, and better decision-making.
- Quality Management should be proactive, not reactive. Strengthening quality management requires a strategic shift towards continuous improvement, proactive risk management, and a deeply ingrained quality culture.
- An eQMS will help ease most of your headaches. A well-integrated eQMS not only reduces manual errors and compliance risks but also provides real-time insights, enabling more informed decision-making and long-term operational success.
Conclusion
Here at Scilife, we’ve been helping pharmaceutical organizations of all shapes and sizes turn their QMS from a chaotic mess into a competitive advantage.
We know that quality is at the heart of producing life-saving, effective, and safe products, and patient safety is always the top priority. That’s why we help you win over your organization for quality and build the strong quality culture that you always wished for. At the core of our approach is our smart QMS software for pharma, designed to simplify quality management, improve collaboration, and help you stay compliant with confidence.