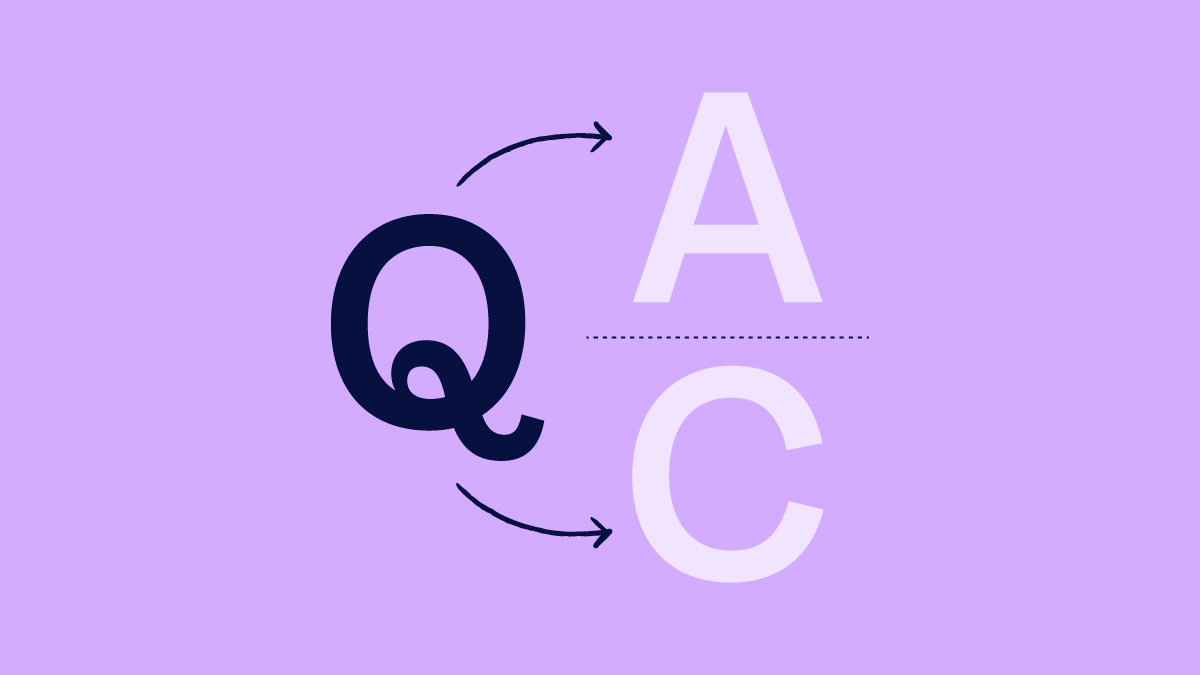
QA and QC processes are inseparable parts of the overall Quality Management System (QMS), and they are often used interchangeably. However, while these processes feature some overlap, it’s essential to note that they are two separate entities and take place at different times. Elements of the QMS may not be specifically composed of QA or QC activities and responsibilities, but instead involve a combination of the two.
Both QA and QC play vital and distinct roles in the health of life sciences companies. As such, it’s good to know the difference between these two processes. According to ISO 9000:2015 – Quality Management Systems – Fundamentals and Vocabulary, QA and QC are both part of the QMS yet focus on different subjects. QA activities mostly focus on providing assurance that quality requirements will be fulfilled, while QC activities focus on actually fulfilling quality requirements.
Understanding the roles of QA and QC can help your organization improve each process and deliver the best possible products. To effectively manage your quality processes—including Quality Assurance and Quality Control activities—you need to implement a QMS according to ISO standard requirements. If you're a medical device company, you've probably known or already implemented the ISO 13485 Quality Management System within your organization; however, other life science organizations might implement ISO 9001, which is another QMS standard.
What is Quality Assurance?
Quality Assurance consists of a series of activities carried out by the organization's QMS in order to confirm the product meets quality standards. In short, QA is a pre-planned process that defines the product in its development stage and determines whether it meets the necessary requirements.
The quality assurance process is part of the organization’s overall quality management. In the QA stage, all activities involved in your quality management plan should verify that your product is ready to be approved and get through the manufacturing process.
Assurance has two purposes: internal and external. The internal role of QA involves management, while QA’s external role pertains to the customer, government, agencies, regulators, notified bodies, and third parties.
What is Quality Control?
The Quality Control process features a series of operational techniques and activities needed to meet the parameters of a product's quality and verify that the product is safe and effective after production. In simple terms, the QC process is the inspection stage of the QA process.
Typically, the QC process is designed to help teams identify deficiencies in the product and eliminate them in an effort to comply with the organization’s quality standards.
All elements involved in product development should be considered during the review. The product must undergo testing to identify the deficiency right after it’s produced. If any deficiency is disclosed, it should be documented and shared with management, so that they can decide whether to approve and release the product or reject it.
If you want to dive deeper into the basics of quality and quality management systems, be sure to watch the video below!
Differences between Quality Assurance and Quality Control
Although we were quite general in our explanation of both terms, many still find them confusing when listing related tasks. Here are some activities involved in each concept so that you can learn to recognize the differences between QA and QC.
The 5 major differences between Quality Assurance and Quality Control
To provide the full picture, we’re going to examine the five major differences between quality assurance and quality control. The two processes share common goals but work interchangeably. Let’s take a closer look at what they are.
1. Proactive (QA) vs. Reactive (QC)
The QA process is proactive. Its goal is to establish a framework for minimizing issues from the beginning—preventing defects before they arise via process design. For example, the QA process documents standard operating procedures (SOPs) according to ISO standards (ISO 9000, and ISO 13485).
The QC process is reactive, and its purpose is to determine defects in product quality after they’ve occurred. It tests products to ensure they meet the QA-defined requirements. If any quality issue is identified, then several (preventive and corrective) actions need to be taken in order to fix it. Additionally, the outputs of the non-confirmed product can trigger a QA step in order to evaluate and investigate the issue further. The idea behind this is to identify the root cause of the problem and improve the current process to avoid similar issues in the future.
To summarize, QA is proactive, while QC is reactive. Additionally, QA takes place during the development of the product, while QC takes place after the final product has been produced.
2. Process (QA) vs. Product (QC)
QA is process-oriented, and it primarily focuses on processes and procedures for improving quality and preventing quality defects before they occur.
QC is product-oriented and focuses on products by determining quality defects in finished products that might affect customer satisfaction. Here are a few examples of each type of activity:
3. System (QA) vs. Parts (QC)
QA systems primarily include procedures and methods that are defined using ISO standards and/or regulatory requirements, while QC systems measure parts—which can be outputs of the system or used to create the final product (for example, raw material from a supplier). The QA system aims to ensure inputs are always safe and effective (for example, supplier audits).
4. Creation (QA) vs. Verification (QC)
The QA process features the definition of standards for each production step—from design, manufacturing, assembling, packaging, storage, and distribution, to marketing and sales. The objective is to consistently produce high-quality products.
QC, meanwhile, involves measuring activities to verify the finished product before distribution.
5. Entire Team (QA) vs. Dedicated Personnel (QC)
The QMS is the responsibility of the Quality department—specifically, the leadership of the team—while QA activities consist of standards for training, documentation, and review throughout the team. QA activities are therefore performed by the entire team. They represent an organization-wide effort whereby each team member must follow the defined SOPs.
QC is the responsibility of specific personnel within the organization. These individuals must follow SOPs to perform QC product testing.
Similarities between Quality Assurance and Quality Control
Organizations always want to produce high-quality products that deliver maximum customer satisfaction. While both processes play different roles in a QMS, they ultimately share the same goals and objectives.
1. Policies, procedures, and methodologies
Both processes follow standards defined by the organization to achieve high quality, but they each feature a unique approach.
2. Securing high-quality product
There should be several QA and QC steps in place in order to release a high-quality product. QA activities guide organizations on how to do this, while QC helps organizations to ensure their finished product complies with all the necessary requirements.
In this way, both QA and QC help to deliver a high-quality product to the customer. This is important because having satisfied customers can help organizations sustain their position in the market.
3. Preventing major issues
Defects can be minor, major, or massive disruptions. The cost and time needed to fix the problem correlate with how early you identify the defect. Problems mitigated in earlier steps have lower costs and are typically more fixable. When a defect is identified in later process steps, the cost is usually higher. And when it’s identified by a customer, the solution won’t come cheap.
The crucial role of QA and QC activities is to prevent, identify, and fix issues as early as possible in order to reduce costs.
4. Continuous improvement
QA and QC processes offer opportunities to improve in areas like defect detection, requirements gathering, and customer experience. This means your organization can potentially improve your processes to become more efficient and effective with each iteration.
Benefits of Quality Assurance and Quality Control
QA and QC have the same main purposes, but their activities are performed at different stages—and each takes a unique approach. Both, however, are crucial and complementary. Here are some of the benefits of QA and QC:
- Deliver a high-quality output
- Eliminate waste
- Increase operational efficiency
- Provide customer satisfaction
- Ensure less rework and after-sale support
- Encourage a high level of confidence and a motivated team
Quality tools for process improvement
Generally, there are three main techniques involved in the quality control process. These techniques include inspection, statistical sampling, and seven basic tools of quality.
Inspection involves physically examining the deliverable for any defects to see if it matches the requirements. In statistical sampling, you select a random number of items from a batch and inspect them for defects and conformance issues.
Quality pros have many names for these seven basic tools of quality, which were initially outlined by Kaoru Ishikawa, a professor of engineering at Tokyo University, and the father of “quality circles.” Start your quality journey by mastering these tools, and you'll have a name for them too: indispensable.
The seven basic tools of quality include a scatter diagram, control chart, histogram, checklist, Pareto diagram, cause-and-effect analysis, and flow chart. These tools are designed to help you find defects and promote conformance of the product.
1. Cause-and-Effect Diagram
Also known as an Ishikawa or fishbone diagram, is a diagram used to identify many possible causes of an effect or problem and sort ideas into useful categories.
2. Checklist
A structured form for collecting and analyzing data; a generic tool that can be adapted for a wide variety of purposes.
3. Control Chart
A graph for studying how a process changes over time—comparing current data to historical control limits, resulting in conclusions on whether the process variation is consistent (in control) or unpredictable (out of control, affected by special causes of variation).
4. Histogram
The most commonly-used graph for showing frequency distributions, or how often each different value in a set of data occurs.
5. Pareto Chart
A bar graph that shows which factors are most significant.
6. Scatter Diagram
Graph pairs of numerical data, with one variable on each axis, designed to identify a relationship.
7. Stratification
A technique that separates data gathered from a variety of sources so that patterns can be seen (some lists replace stratification with a flowchart or run chart).
Recommended learning: Discover more risk assessment and quality tools in our detailed guide here!
The role of QA and QC processes within your QMS – are you getting the balance right?
When you decide to implement a QMS in your organization, the QA and QC processes are not optional—you need to include both. Additionally, neither one is more valuable than the other. By using both processes when needed, the output of the QA should feed the QC activities; the output of a QC activity can feed the QA activity as well.
QA focuses on processes and systems that prevent defects by ensuring procedures are well-defined and followed. QC, on the other hand, focuses on detecting and correcting defects through inspection and testing of products or outputs. Together, QA ensures the right process is followed, and QC verifies the results.
For instance, say you’ve defined the procedures, or the methods for the product according to standards as a QA activity. Then, you simply verify the product by using those procedures. Furthermore, if you identify a defect in the product, then you need to investigate the nonconformance as a QA activity. As you can see, an output can serve as an input of the other process.
This means that maximizing the effectiveness of your quality management system depends on maintaining a fine balance of quality assurance vs quality control activity. Easier said than done, many quality professionals in the life sciences often struggle to get this balance right which can result in significant issues that impact product quality, patient safety, and overall business performance.
What happens when Quality Control is lacking?
Without strong QC, the risks are severe, far-reaching, and costly. Companies fall into a cycle of unrealistic procedures that don’t align with actual operations. Critical defects and weaknesses are missed, leading to serious consequences such as patient harm or even fatalities. Customers lose trust, become dissatisfied, and take their business elsewhere. Meanwhile, auditors uncover a growing list of nonconformances. Regulatory fines stack up. Product recalls loom. Facility shutdowns become a real threat.
In short, the consequences of poor QC can quickly turn your quality management system into a disaster.
What happens when Quality Assurance is lacking?
Without strong QA, your company can quickly fall behind competitors, miss growth opportunities, and risk long-term success. Even if product quality remains steady, the ability to refine and adapt processes begins to slip. Proactive audits don’t happen. Employees miss out on critical training. Process documentation grows outdated.
The result? Your business becomes static and struggles to stay competitive. Over time, compliance risks mount as evolving regulations outpace your systems, and demonstrating continuous improvement to auditors becomes a challenge. Strong QA isn’t just a nice-to-have—it’s what keeps your company sharp, agile, and ahead of the curve.
How an eQMS help you get the balance between QA and QC right
As we know, both QA and QC play a key role in an organization’s QMS for end-to-end quality processes. But your organization shouldn’t have to choose between QA and QC—they’re most effective when working together.
The truth is that QA and QC complement each other best when integrated into a single electronic Quality Management System (eQMS). This provides your business with a unified source of quality trust and strengthens connectivity across all operations—a fact that more and more organizations are recognizing.
With a cloud-based QMS like Scilife, both QA and QC processes are seamlessly integrated to ensure quality is assured and controlled throughout the entire product lifecycle. From document control and training to CAPA management and complaint handling, Scilife supports every step of your quality journey.
Our eQMS achieves this by automating repetitive tasks, monitoring activities in real time, and effectively managing all critical areas essential for maintaining exceptional quality in both products and processes. By streamlining operations and reducing the risk of human error, we help you ensure consistency, accuracy, and efficiency across your quality management workflows.
Conclusion
Every organization aims to deliver an exceptional customer experience—because a great customer experience translates into satisfied customers. Nowadays, both companies and users are becoming increasingly sensitive to quality, avoiding products that do not meet quality standards. Quality Assurance and Quality Control are processes that, when they are well-implemented and understood by the whole team, will allow you to succeed in providing quality products and services that address your customers’ needs and concerns.
Striking the right balance between QA and QC is essential for life sciences companies to ensure product quality, foster continuous improvement, and mitigate risks tied to regulatory non-compliance and patient safety.
If managing QA and QC feels like a challenge, we’re here to help! Our user-friendly, scalable platform is designed to simplify your quality management processes and make those headaches a thing of the past.
Discover how our Smart QMS can help you achieve the perfect harmony between QA and QC!