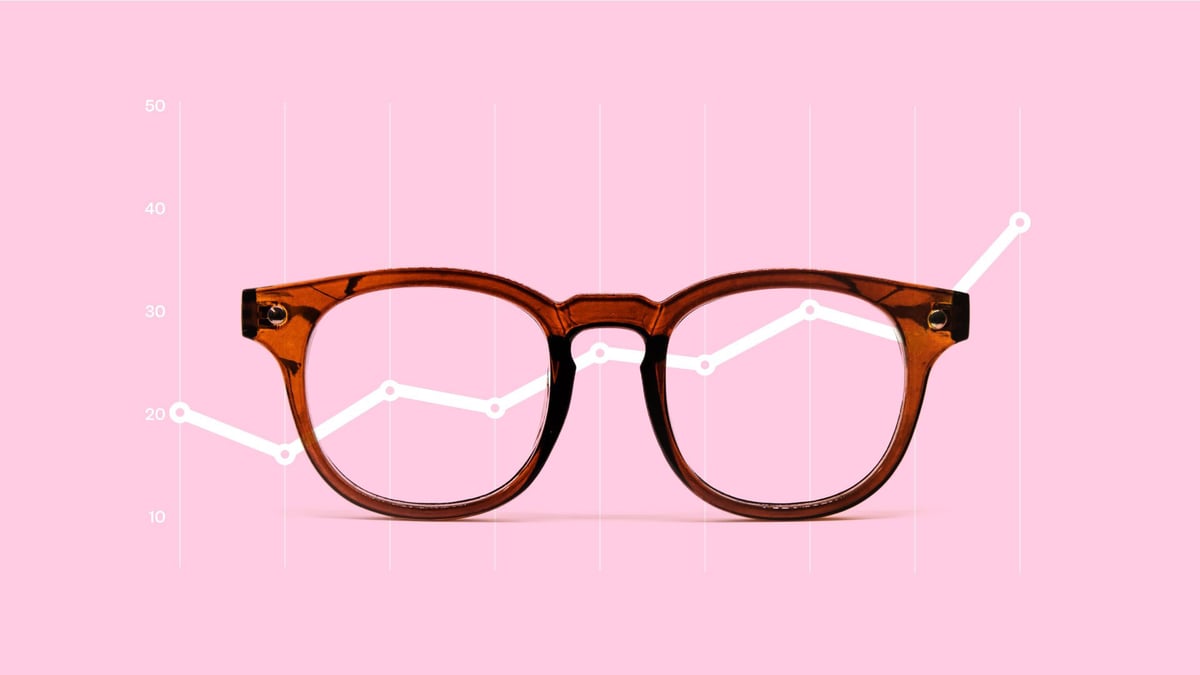
Corrective and Preventive Action (CAPA) management is a vital process of any Quality Management System. CAPAs are the necessary steps that must be taken to eliminate causes of non-conformities or other undesirable situations and lie at the heart of process-level improvement. Managing these effectively is crucial, and that requires several best practices.
The main part of effective CAPA process management is of course accurately logging, assigning, approving, and then implementing CAPAs. However, the review stage of any CAPA process and CAPA quality to assess effectiveness is equally important in a continuous improvement cycle and is sometimes overlooked in an organization.
Reviewing your CAPA Process
Verify Effectiveness
Assuming that you’ve already implemented a CAPA management system as a part of your QMS, here’s how you can verify your CAPA process and CAPA quality and how you can evaluate the overall status and health of your CAPAs.
The CAPA process proceeds step by step, and each step needs the proper inputs (which are actually outputs of the previous step). The employees you’ve assigned as your CAPA team will use the most suitable tool(s) to conduct the CAPA management process. Each CAPA process report should include one final step to verify the actions in place.
What is Verification of Effectiveness (VoE) &
why is it crucial in your CAPA process?
Nonconformities can occur in any highly regulated industry, which of course includes Life Sciences industries such as pharma, medical devices, and biotech. In order to solve the nonconformity, your organization should assign a coordinator and also a team to handle it (preferably multidisciplinary). In most cases, your designated CAPA team will focus to solve the problem and prevent the recurrence by planning Corrective Actions (CAs) and Preventive Actions (PAs) using Root cause analysis techniques.
Then, the CAPA process and CAPA quality need to be verified as effective and completed according to the ICH Q10 step3.2.2. The guideline here states that “CAPA should be used and the effectiveness of the actions should be evaluated.” For this reason, your QA and the CAPA team should perform effectiveness checks in order to verify the effectiveness of the actions put into place, to check if they’ve actually eliminated the issue.
How do you conduct a Verification of Effectiveness (VoE) process?
When your team plans several actions (CA or CA and PA) which are addressed to the Root cause(s) of the nonconformity, it’s time to implement the planned actions respectively.
After all of the actions are implemented, you can perform your verification of the Implementation (VoI).
What is Verification of Implementation (VoI)?
The verification of the Implementation (VoI) phase is often confused with the Verification of Effectiveness (VoE) phase of the CAPA process; it's important to distinguish that they are separate phases.
The VoI phase documents that the actions (containments, corrections, CAs, and PAs) were indeed implemented as planned in the CAPA planning phase, and the VoE phase checks if these actions were actually effective.
A few examples of VoIs include:
What is a Verification of Effectiveness Plan (VoEP)?
The Verification of Effectiveness Plan (VoEP) is the planning step of the Verification of Effectiveness process. In this stage, you establish and define the criteria for how your team will verify that the CAPA was indeed effective.
The SMART technique is a useful tool that can help you to establish your Verification of Effectiveness Plan (VoEP).
What is the SMART technique and how is it used in a Verification of Effectiveness Plan (VoEP)?
To make sure your Verification of Effectiveness Plan is clear and realistic it should be all of the following:
-
- Specific (simple, sensible, significant)
Is your VoEP unambiguous, clear, and focused?
- Specific (simple, sensible, significant)
-
- Measurable (meaningful, motivating)
Is quantifiable data being used to assess effectiveness in your VOEP?
- Measurable (meaningful, motivating)
-
- Achievable (agreed, attainable)
Is your VoEP feasible and practical?
- Achievable (agreed, attainable)
-
- Relevant (reasonable, realistic and resourced, results-based)
Is your VoEP appropriate considering the level of risk?
- Relevant (reasonable, realistic and resourced, results-based)
-
- Time-bound (time-based, time-limited, time/cost limited, timely, time-sensitive)
Does your VoEP have a realistic deadline?
- Time-bound (time-based, time-limited, time/cost limited, timely, time-sensitive)
Examples of checks on a VoEP checklist include:
-
- The problem has not recurred in the last three production lots
- The problem has not recurred in the last three months
- The first pass yield is >99 percent
- The scrap rate will decrease by 5 percent (say, from 15 percent to 10 percent)
- The problem has not recurred in the last three production lots
The planned criteria should be reviewed and documented in the VoE (verification of effectiveness). If all actions meet those criteria, it means that your actions are taken and implemented effectively. The effectiveness should be objective and the decision should be made by your team including QA and Manufacturing managers/responsible persons. To mitigate risks, evaluate your taken actions after a defined period of time using the defined evaluation method (criteria).
Note: A CAPA should only be closed once the verification of effectiveness has been completed. If a CAPA was found to be ineffective, then open a new CAPA and reference the original one. |
Best Practices in creating an Effectiveness Checklist
The most vital step of an effectiveness checklist is making it an obligatory step of your CAPA management process! The following best practices help your team prevent skipping this step once the actions are in place.
-
- The effectiveness checklist criteria should be defined in advance in order to be consistent in each CAPA report, however, it should also be adaptable to different conditions.
- The verification of the Effectiveness Plan (VoEP) should be prepared with a risk-based approach. If the risk is higher, more effectiveness checks should be planned.
- A successful Effectiveness check doesn’t just mean that your actions are taken effectively. It also means that the problem is eliminated by the actions taken. You should check the effectiveness of the process itself in order to verify.
- Plan time before verifying the effectiveness of a CAPA process in order to collect enough data to evaluate its effectiveness. However, this allocated time should not be too long, as that can hinder the company or become a drain on resources.
- The effectiveness checklist criteria should be defined in advance in order to be consistent in each CAPA report, however, it should also be adaptable to different conditions.
Linking CAPAs to Management Reviews
CAPA reports are important inputs of the Quality Management Review meetings, therefore CAPA-related KPI parameters should be presented and reviewed. These parameters could be following but not limited to;
-
- CAPA aging
- Number of open CAPAs
- Risk levels of CAPAs
- The current phase of CAPAs
- Overdue CAPAs with their reason
- CAPA trends breakdown by root causes, environment
- Percentage of extensions
- CAPA aging
Another important reason to review CAPAs as a part of management review meetings is to enable your QA personnel to initiate new CAPAs by actions that are discussed in that meeting.
All actions of the meeting become a CAPA and will be discussed as a part of these meetings.
How Periodic CAPA reviews help take preventative actions
Your organization can decide to review CAPAs thoroughly in a separate meeting. You should define the following information in your procedure:
-
- Define review period (Monthly, quarterly, once every six months)
- Define what will be reviewed in which meeting (MRM or Periodic CAPA review meeting)
- Define who should attend this meeting
- Define review period (Monthly, quarterly, once every six months)
-
- Define review parameters:
- Raw number breakdowns by previous periods/ months, years, etc.
- Split numbers of open CAPAs as per categories
- Pie charts for Root cause categorization as per a fishbone diagram
- Open, close, cancellation (if any) rate by the time, overdue rates
- Open and close rate by time, overdue rates
- Effectiveness rate breakdown by closed CAPAs
- Breakdown by location/equipment where the incident occurred
- Trending analysis of test results of important quality control steps
- Root causes of Complaints
- Raw number breakdowns by previous periods/ months, years, etc.
- Define review parameters:
-
- Consider and define parameters that are important for your QMS such as:
- Complaints breakdown by product
- More than 3 Major internal audit findings are observed in the same subsystem but by different audits.
- More than 3 Critical external audit findings are observed in the same subsystem but by different audits.
- More than 3 product recalls which were caused by the same root cause
- Complaints breakdown by product
- Consider and define parameters that are important for your QMS such as:
-
-
- Product recall without CAPA reports
- Overdue on the Revalidation More than 3 times
- Approval performance of the batch release activities
- Recalls caused by rework/relabelling
- Overdue on calibration dates, using equipment that is not recalibrated on time
- Contamination(pest control) of the same area by 3 consecutive months
- Product return that could cause product recall
- Product recall without CAPA reports
-
Even though it's important to make periodic meetings, the parameters play a major role in reviews. Reviewing CAPAs periodically using the right parameters lets you see the full picture. In this way, you can foresee the possible nonconformity by the density of the similar parameters, root causes, locations, equipment, etc. Once you foresee a potential nonconformity, you can initiate a Preventive Action (PA) report and take those preventive actions.
|
As you see in this example, once you have the first two CAPAs, you are able to determine that those 2 different CAPAs occurred based on the same or similar root causes. It’s important to set monthly CAPA meetings as well as to conduct a deeper analysis if you have more than one similar CAPA. In this way, you can prevent the third CAPA by initiating a PA report and eliminating possible causes.
If your parameters did not cover the entire process, then you are not able to determine the underlying root cause.
To Sum it Up:
CAPA reviews are all important!
By undertaking CAPA effectiveness checks, you can track, trend, and fix deviations that occur along with any point in a process. Robust CAPA action plans and timing effectiveness checks appropriately help foresee and fix issues that may cause deviations. A strong quality team that performs these CAPA process effectiveness checks is vital to making sure that it’s all done on time and that effectiveness checks are actually improving the process. When done well, these checks are a demonstration of your organization’s commitment to quality and compliance.
Sounds like a hassle?
Scilife’s CAPA Software can help!
If the mere thought of planning periodic reviews for each of your CAPAs gives you a headache, don’t worry, Scilife can help! Our dedicated CAPAs solution in the Scilife platform takes care of reminding and notifying the right people at exactly the right time when it comes to CAPA process reviews. Simply program follow-up checks when logging any CAPA on the templates provided by the module, and you’re all set!
Finally, chaotic CAPA processes can transform into smooth cascades leading to continuous improvement throughout your organization.