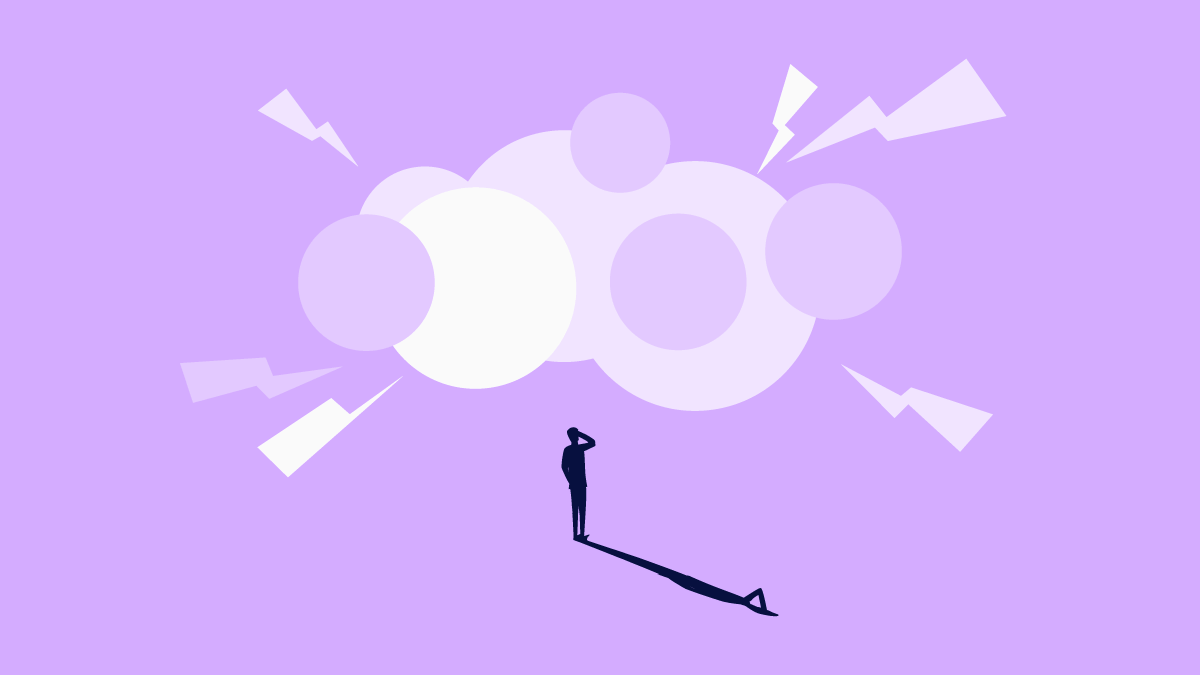
In the life sciences industry, a robust Quality Management System (QMS) is all-important for achieving compliance, sustaining operational efficiency, and safeguarding public trust. A QMS underpins every aspect of quality control, from adhering to stringent regulatory requirements to guaranteeing product consistency and safety. However, when cracks begin to appear in your quality management process, the consequences can be severe, including product recalls, compliance violations, and reputational damage. Addressing these issues proactively is far more practical than reacting to failures after they occur.
This blog explores the main warning signs of a failing QMS and provides actionable strategies to bring your system back on track. With the right approach, you can transform your QMS from a reactive process to a proactive driver of quality excellence, guaranteeing long-term success in an increasingly competitive and regulated industry.
The importance of a QMS in life sciences
A QMS is more than just a regulatory requirement, it is the backbone of operational excellence in industries like pharmaceuticals and medical devices. It makes certain that organizations consistently deliver products that meet both regulatory requirements and customer expectations. A well-implemented QMS nurtures a culture of continuous improvement and drives innovation. Failing to preserve your QMS can lead to cascading problems, from inefficiencies in production to compliance risks and customer dissatisfaction.
7 warning signs your quality management process is hanging by a thread
1. You are not audit-ready
Being unprepared for audits is a clear indicator of a failing QMS, often resulting from misaligned processes and outdated documentation. Regulatory frameworks like ISO 13485:2016 emphasize risk-based thinking and continuous improvement, both of which are important for supporting compliance and operational efficiency. Without adherence to such standards, organizations face delays in market access, regulatory penalties, and reputational damage.
A study on partnerships with global medical device companies underscores the importance of ISO 13485 compliance, ranking it as the most important factor for success. This finding highlights the necessity of aligning quality systems with global audit expectations to keep a competitive edge. Regular internal audits, up-to-date documentation, and a proactive approach to quality management can help organizations achieve audit readiness and avoid costly disruptions.
2. Dependence on paper-based systems
Despite the availability of advanced digital solutions, many organizations continue to rely on outdated, paper-based systems for managing quality processes. These systems are prone to errors, inefficiencies, and compliance risks. Paper-based documentation is easily lost or damaged and makes data retrieval cumbersome, especially during regulatory audits or inspections.
Transitioning to an electronic document management system (EDMS) is a great step toward modernizing your QMS. An EDMS enhances document control, supports compliance with regulatory standards like FDA 21 CFR Part 11, and simplifies workflows with automated approvals and version updates. Implementing a cloud-based QMS further allows for remote access and real-time collaboration, making your quality management process more agile and resilient.
Recommended learning: Still not convinced you need a cloud-based QMS? Discover all the advantages that you will gain by moving away from paper in our article.
3. Employees lack awareness of quality policies
A lack of employee awareness about quality policies and procedures is a major indicator of a failing QMS. When staff are inadequately trained or uninformed, the risks of non-compliance, operational errors, and regulatory breaches multiply. A recent study highlighted the importance of adhering to harmonized standards like ISO 13485:2016, which stresses the need for a unified approach to quality management and clear communication of policies across all levels of the organization. Without these safeguards, the potential for inconsistency grows exponentially.
To address this, organizations must invest in comprehensive training programs that lead to every employee understanding and aligning with quality standards and SOPs. Implementing a training management system can streamline the creation, dissemination, and tracking of training initiatives. Providing accessible, up-to-date quality documentation creates a culture of accountability and empowers employees to contribute to organizational quality objectives.
4. Outdated SOPs and training materials
Using outdated standard operating procedures (SOPs) or training materials can severely compromise your organization's QMS. Regulatory agencies like the FDA require up-to-date SOPs to be readily accessible at points of use.
A review of lifecycle management practices in the medical device sector underscores how fragmented documentation systems exacerbate these challenges. Organizations using disconnected or manual systems struggle with version control and consistency, leading to errors. Transitioning to a centralized document control system that seamlessly updates and distributes SOPs is key to mitigating these risks. Integrating training materials within your QMS allows employees to have real-time access to the latest procedures and regulatory updates.
5. Quality is treated as a departmental responsibility
A siloed approach to quality management, where it is seen as the sole responsibility of the quality team, can hinder your organization’s ability to achieve true operational excellence. Quality must be embedded into every department, with cross-functional collaboration providing a holistic approach to process improvement and compliance.
Support a culture of quality by integrating quality metrics into every department’s KPIs. Cross-functional training sessions and collaborative platforms can help break down silos and encourage shared accountability. A well-implemented QMS can facilitate this by providing a unified framework for quality management across all departments.
6. CAPA processes are inefficient
Corrective and Preventive Actions (CAPAs) address and prevent quality issues, but ineffective CAPA processes are a major red flag. Common issues include delayed investigations, insufficient root cause analyses, and unresolved quality events. Regulatory bodies frequently cite CAPA deficiencies during inspections, making this an area of high risk.
Modern CAPA management tools can automate workflows, establish timely resolution of quality events, and provide detailed analytics for root cause identification. By integrating CAPA processes with your QMS, you can track progress and continuously improve your quality management efforts.
According to McManus's foundational study on Lean methodology, implementing structured Lean tools like Value Stream Mapping can reduce product development lead time by 50–75%. This highlights the potential of Lean approaches to streamline processes, including CAPA activities.
7. Increasing customer complaints and product recalls
Rising customer complaints and frequent product recalls indicate significant gaps in your quality management process. These issues not only harm your reputation but also lead to financial losses and strained customer relationships.
A study published in the Journal of Pharmaceutical Research International underscores the importance of robust compliance frameworks and monitoring systems in retaining high-quality standards and encouraging trust in regulated industries. The research highlights that, without these safeguards, organizations face heightened risks of increased customer complaints and diminished stakeholder confidence.
Establish a strong complaints management system to monitor and resolve issues promptly. Conduct root cause analyses for recurring complaints and use insights to implement preventive measures. Trend analyses and customer feedback loops can further enhance your ability to identify and address quality problems proactively.
Scilife tips to saving your QMS
Conduct a quality maturity assessment
Building a strong QMS requires assessing where your processes currently stand. Scilife offers a Quality Management Maturity Scan, a quick tool designed to help organizations evaluate their quality processes and identify opportunities for improvement. The scan places businesses on a five-level Quality Management Maturity Curve, starting with Level 1: Uncertainty, where compliance is the main focus, to Level 5: Certainty, where quality is seamlessly integrated into every aspect of operations and becomes a competitive advantage.
Leverage modern technology
Transitioning to an electronic Quality Management System (eQMS) can overhaul your approach to quality management. An eQMS streamlines workflows, automates routine tasks, and provides real-time insights into your quality processes. This enables proactive decision-making and provides compliance with regulatory requirements.
Foster a culture of quality
Quality should be everyone’s responsibility, not just that of the quality team. Encourage cross-functional collaboration, integrate quality metrics into departmental goals, and provide ongoing training to instill a culture of continuous improvement.
Proactive versus reactive
Move from a reactive to a proactive approach by deploying predictive analytics and real-time monitoring tools. Anticipating quality issues before they escalate allows your organization to address them competently.
Conclusion
Understanding your maturity level is a practical starting point. To advance, an eQMS like Scilife can help transform your processes by centralizing documentation, automating workflows, and improving training practices. These improvements enable you to move from reacting to quality problems to proactively preventing them, paving the way for better operations and alignment with industry standards.