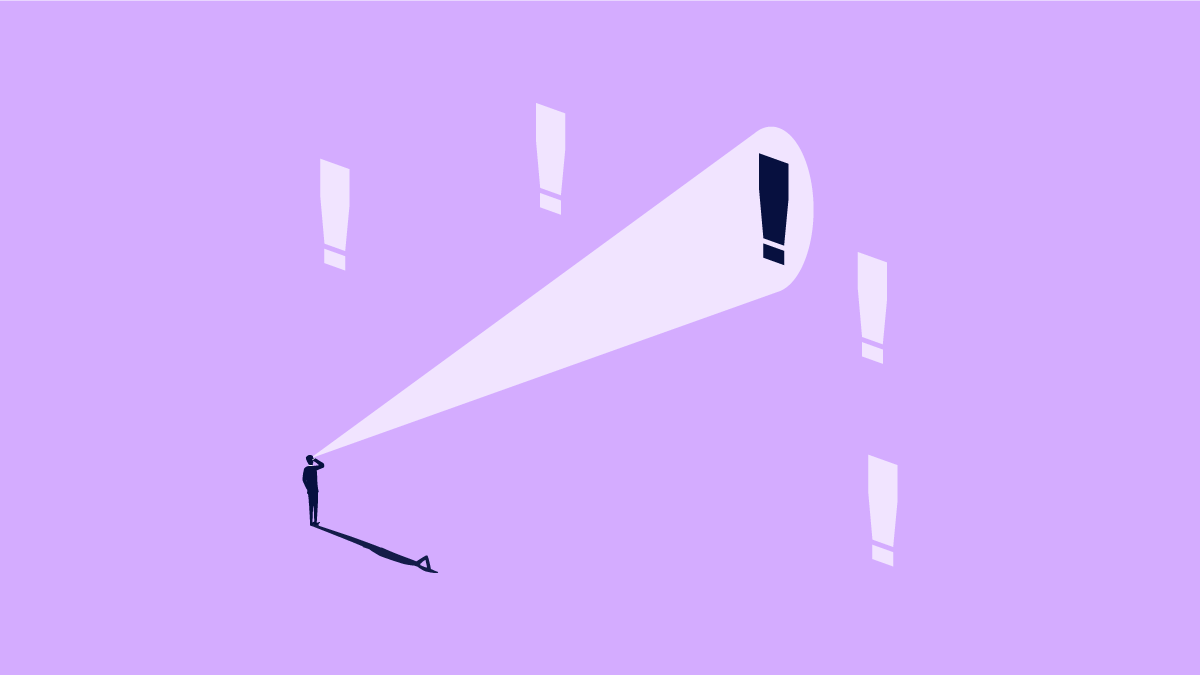
It is almost impossible to work in the medical device space without hearing the term ISO 13485. But what is it? And how can you avoid mistakes during scoping and implementation and ensure the continued availability of your products on the market? That's precisely what we will teach you in this blog!
What is ISO 13485?
ISO 13485 is an internationally recognized standard that sets out the requirements for quality management systems (QMS) in the medical device industry. Established by the International Organization for Standardization (ISO), ISO 13485 ensures that organizations involved in designing, producing, installing, and servicing medical devices consistently meet regulatory requirements and customer expectations.
ISO 13485 focuses on risk management, process control, and the maintenance of effective processes, emphasizing the importance of a robust quality management system in ensuring the safety and efficacy of medical devices. Compliance with ISO 13485 helps companies streamline their operations, improve product quality, and facilitate market access globally by aligning with various regulatory frameworks, such as the FDA's Quality System Regulation (QSR) in the United States and the European Union's Medical Device Regulation (MDR).
Source: Medical Device HQ
Achieving ISO 13485 certification signifies a commitment to quality and patient safety. While not mandatory in the EU or the US, compliance with ISO 13485 is the simplest way to achieve the highest quality of your QMS.
The implementation of an ISO 13485 quality management system can be considered a discipline. So, what hurdles must you overcome to make your QMS the best it can be? Let's take a look!
Recommended learning: Learn the ins and outs of QSR and ISO 13485 harmonization and how to prepare for QMSR effectively.
Mistake 1: not performing internal audits
Even if you have the best, most complete system in the world, failure is inevitable without testing. Just like we verify and validate our medical devices, we must also put our QMS to the test. This is what internal audits are for!
Internal audits are crucial for the effective implementation of ISO 13485 for several reasons:
- Internal audits help verify that your quality management system (QMS) meets ISO 13485's requirements. This ensures that all processes, procedures, and documentation meet the specified standards.
- Regular internal audits identify areas for improvement within the QMS. By detecting non-conformities and potential risks early, organizations can implement corrective and preventive actions and foster continuous improvement. Nothing can make you see all the holes in your QMS, like preparing for and sitting through an audit!
- Internal audits prepare organizations for external audits and regulatory inspections. Most people are scared during their first audit. In their second audit, that fear has turned to nervousness. In the third audit, you think, "This is fine, I've done this before. "There's nothing like nerves that'll make you say or do something inconvenient during an audit. Training the audit situation helps employees feel secure and confident during future external audits. It also forces them to review the QMS and know their responsibilities within the system.
- Audits ensure that all necessary documentation and records are maintained accurately, which is essential for traceability, accountability, and compliance with regulatory requirements.
- Findings from internal audits provide valuable insights for management reviews, aiding in strategic decision-making and resource allocation to strengthen the QMS.
Mistake 2: not implementing a completely risk-based process
ISO 13485 clearly emphasizes risk-based processes. Even so, some manufacturers treat their risk management as something separate from their other QMS processes, which is a mistake. Regulatory authorities want to reduce risk to the patient and public health so they will look for flaws in your risk approach and framework. Risk should be a red thread that runs through all your documentation, and any decisions made in the manufacturing process should be based on and justifiable through your risk management documentation. Your risk management file might be your most important QMS document!
Mistake 3: not treating CAPAs with the respect they deserve
Once you've started conducting internal audits, you may realize that the CAPA section of the audit is where you spend the most time. It's not just you – many manufacturers struggle with implementing adequate and complete CAPA processes. While some get stuck on building effective processes, most manufacturers struggle with ineffective investigations. From employees not understanding root cause analysis correctly to not defining completion deadlines or not finishing by the deadline to CAPAs not properly preventing the same thing from happening in the future - we've seen it all.
ISO 13485 audits almost always delve deeply into the CAPA process, so it's vital for success to ensure that your CAPAs are well-documented, well-researched, and completed in time and that the problem is prevented from happening again.
Mistake 4: Not handling customer feedback appropriately
Customer feedback can help you avoid product recalls, ensure continuous device improvement, increase customer satisfaction, cement your regulatory compliance, ensure patient safety, and increase your lead in the market - if you handle it appropriately.
ISO 13485 emphasizes both reactive and proactive customer feedback collection, unlike the FDA in the US, which is traditionally more focused on reactive feedback.
Reactive feedback is received after something has happened with the device, usually because the device doesn't meet the customers' or users' expectations. Complaints are the most common type of reactive feedback.
On the other hand, proactive feedback is feedback a manufacturer has actively sought, such as product surveys or post-market clinical follow-up. Gone are the days when medical device manufacturers could afford to wait for feedback from their users—they must actively elicit feedback and ensure it enters their device lifecycle management.
Mistake 5: doing the bare minimum
It's no secret that regulatory and quality departments are receiving fewer resources. In some manufacturers, one department might handle regulatory and quality matters, with one or two people managing both sides. This is why some manufacturers do what they can to get the ISO 13485 certification, but not a document. They might also seek out certification to gain access to more essential markets.
ISO 13485 is a holistic approach to quality management systems, not a checkbox to get through. Implementing a complete ISO 13485 QMS can:
- Enhance product quality: ISO 13485 emphasizes stringent quality control and management practices, leading to higher quality products that meet safety and performance standards.
- Ensure regulatory compliance: Certification ensures the organization meets international regulatory requirements, facilitating smoother approvals and compliance with bodies like the FDA, EMA, and other national health authorities.
- Enable market access: ISO 13485 certification is recognized globally, enabling more accessible entry into international markets and expanding business opportunities.
Give your risk management a push: The standard's focus on risk management helps identify, assess, and mitigate risks throughout the product lifecycle, enhancing patient safety and product reliability. - Build customer trust and satisfaction: Certification demonstrates a commitment to quality and safety, building customer trust and improving overall customer satisfaction.
Improve operational efficiency: Implementing ISO 13485 can streamline processes, reduce waste, and improve overall operational efficiency (aka cost savings). - Build continuous improvement practices: The standard promotes a culture of continuous improvement through regular audits, management reviews, and corrective and preventive actions (CAPAs).
- Give you a competitive advantage: ISO 13485 certification can differentiate an organization from its competitors, showcasing its commitment to high standards and quality management.
- Facilitate employee engagement and training: The certification process involves comprehensive training and engagement of employees, leading to a better understanding of quality practices and increased workforce competence.
- Improve documentation and traceability: ISO 13485 requires thorough documentation and record-keeping, enhancing traceability and accountability throughout the supply chain.
- Build supply chain confidence: Suppliers and partners view certified organizations more favorably, leading to more robust and reliable supply chain relationships.
- Reduce product recalls and failures: By adhering to stringent quality management practices, organizations can reduce the incidence of product recalls and failures, protecting their reputation and financial stability.
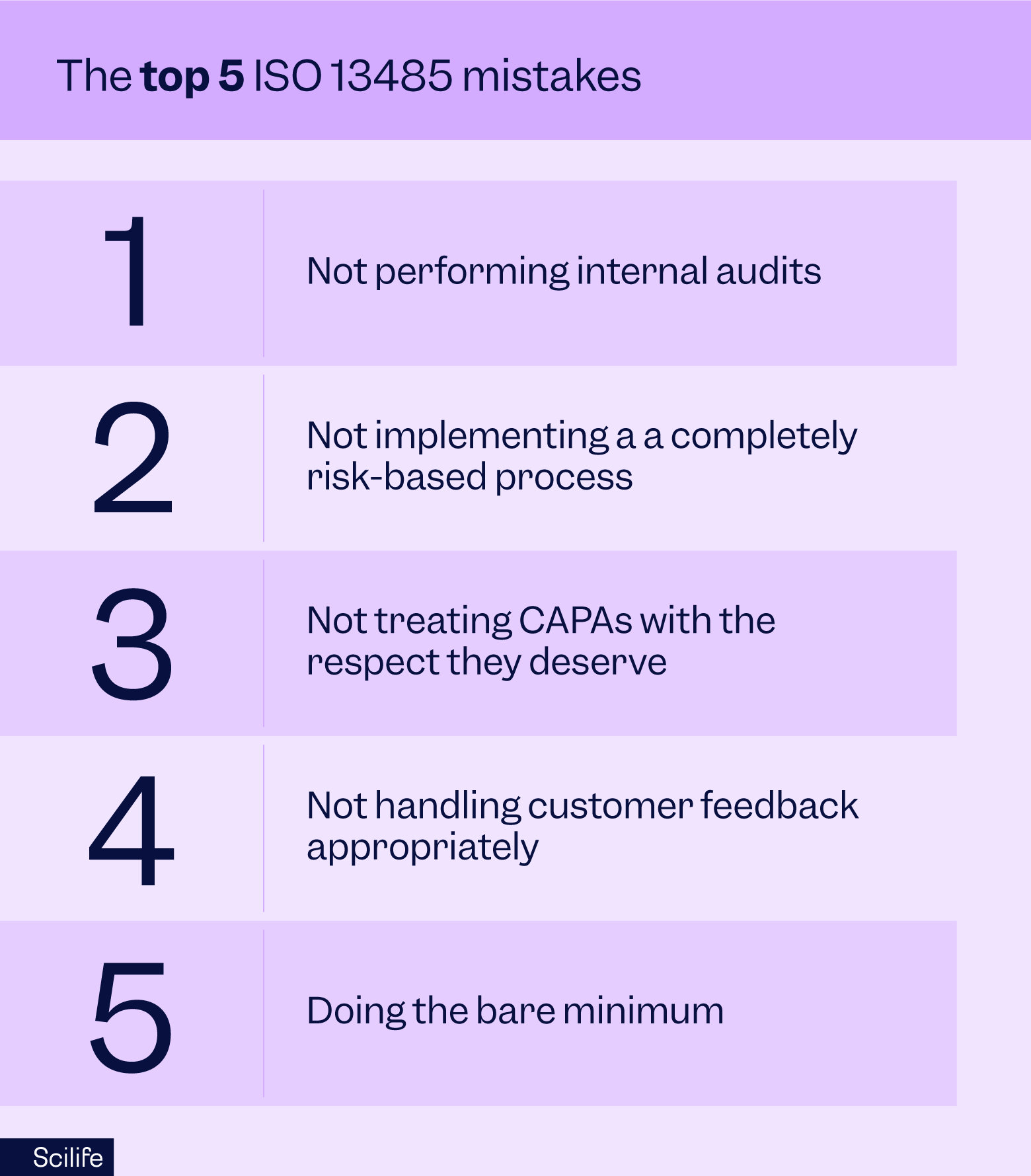
Conclusion
ISO 13485 is crucial, as it specifies requirements for a quality management system (QMS) for medical devices. It ensures consistent design, development, production, installation, and delivery of safe and effective medical devices. Compliance with ISO 13485 demonstrates a commitment to quality and regulatory requirements, facilitating market access and customer trust. It helps manufacturers mitigate risks, improve processes, and enhance product quality. By aligning with international standards, ISO 13485 supports global trade and interoperability, contributing to improved patient safety and satisfaction.