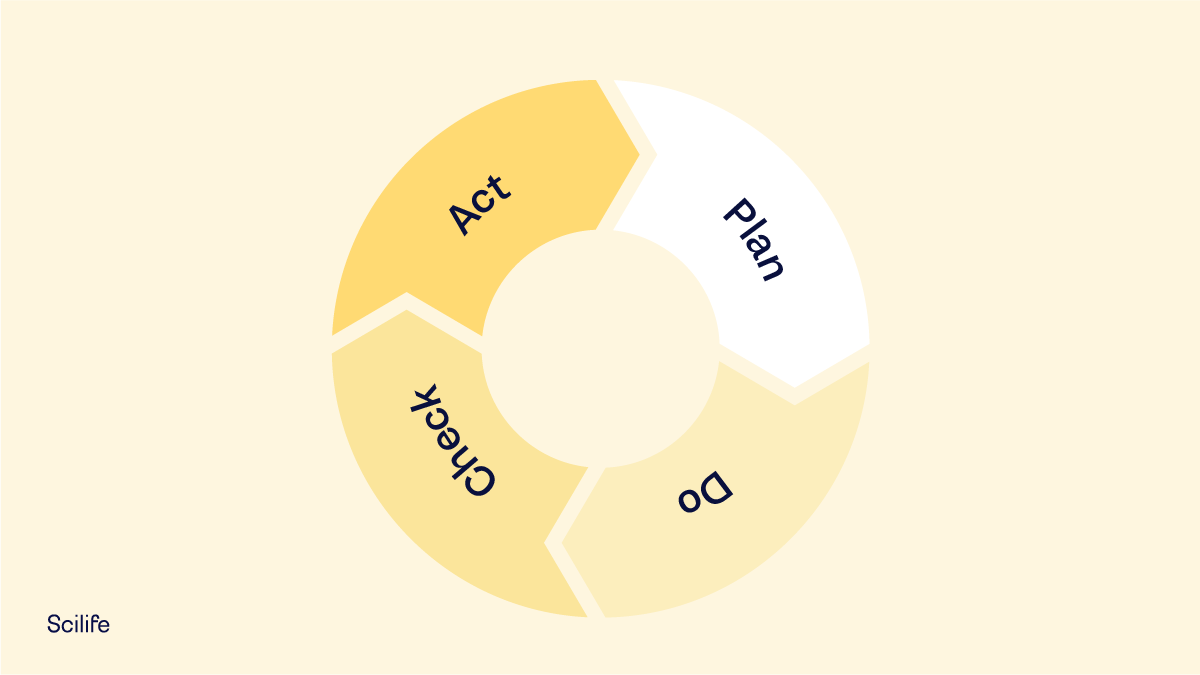
Rigorous quality management is fundamental in all regulated sectors, including pharmaceutical, biotech and medical device industries. A good Quality Management System (QMS) is able to define and organize documents and other processes in a quality-adhering way. Usually, QMS are run through purpose-built software. These programs do much more than basic quality management, which we’ll cover later in this piece. In essence, a QMS provides a structure for various functions within an organization to work in an integrated manner, ultimately delivering the best quality products and services to customers. It’s the cornerstone of quality management.
So, how does an organization implement a QMS and improve their quality management?
Introducing Plan-Do-Check-Act for Quality Management
You might have heard the phrase ‘Plan-Do-Check-Act’. The Deming cycle (also known as the PDCA model) is very commonly used in organizational settings, continuous improvement initiatives, and quality management.
Read about how to ‘Plan-Do-Check-Act’ (PDCA) specifically for continuous improvement on the Scilife blog here.
In quality improvement, the Deming method of ‘Plan-Do-Check-Act’ helps organizations to work through each stage of the process systematically.
Here’s a quick breakdown of the four stages of the cycle:
1. Plan
This initial stage in the Deming cycle for quality management gets a company to define and strategize organizational processes. It’s the first step when it comes to implementing a QMS.
- Define quality: understand the meaning of quality from the customer’s point of view as well as a compliance perspective. Clearly state the specification limits and compliance requirements.
- Define policies and processes: Document the company’s vision, policies, processes and procedures to implement a QMS. This helps map out organizational structure and the key responsibilities of employees in every function. It enables employees to understand what their key deliverables are in terms of quality, and how they can collaborate with employees in other functions.
2. Do
The second stage of the Deming cycle in the ‘Plan-Do-Check-Act’ sequence for quality management is all about doing. It’s time to take and test the necessary steps to carry out the actions for manufacturing the desired quality product.
That means first designing for that quality. As we all know, quality doesn’t happen by chance. quality happens by design. One of the ways of building the desired quality into the product is to ensure that the natural variation in the product is as low as possible, and smaller than the defined quality specification. Scientists and researchers use various statistical and deterministic models to control such variation. This is to ensure that the desired quality of the product will be manufactured consistently and repeatedly, batch after batch.
3. Check
Third in the cycle is checking if the actions that have been carried out produced the desired results. Is the quality of the product up to standard? This question is answered through two major processes:
- Quality Control: testing and/or measuring the key quality performance indicators (KPIs) of the products. A report on test results is then prepared by the quality control team.
- Quality Assurance: Reviewing the documented results and performing cross-checks for any errors before the products are shipped to the customer.
A validated QMS is especially useful in this stage. An eQMS program will help prepare digital reports as well as facilitate review and signature processes for quality control and quality assurance functions. Additionally, good quality management software can monitor key performance indicators with customized dashboards for every product.
4. Act
The final stage of the cycle is about taking action on results. Specifically, acting on non-conformities. Once a company has carried out the planning, doing, and checking stages it’s time to make any tweaks or changes in the process to meet the desired quality of the product. In other words, improvement.
If the KPIs show deviation from expected quality of the product then improvement processes must be planned for and implemented. There’s also opportunity for incremental improvements: after all the philosophy of continuous improvement states there's scope for improvement in every act we do.
In this last stage, it’s important the company creates a record of whether the proposed solution actually solved the problem, and recommends future action.
Quality Management Systems (QMS)
The Deming ‘Plan-Do-Check-Act’ cycle makes it very easy for any organization to implement a strong Quality Management System (QMS).
Nowadays, there are powerful and multifaceted eQMS programs (entirely digital quality management systems) that provide much more than simply organizing quality processes for a company. Such all-in-one QMS software streamlines and optimizes quality, and often even non-quality, procedures to save a company time, money and other resources. For example, providing an easier way to train and assess employees.
Good eQMS software stores data securely in the cloud, freeing up physical storage space but also making access for those who need it easier - the cloud can be logged into from any location and on any device. That opens up collaboration opportunities, speeds up audits, and allows teams to move freely around the globe.
Quality results, policies, quality specifications, compliance requirements and standard operating procedures can be found in a few clicks from a central hub in an eQMS. That enables data transparency and also the useful interlinking of processes like CAPAs and change control.
Most importantly, with QMS software data integrity issues are solved as there is inbuilt digital traceability of actions. This is a leading cause for warning letters from regulatory agencies, so an eQMS removes a big headache here.
Any QMS used in the life sciences, whether fully digital or not, must adhere to the strict regulatory requirements of the industry. To describe the requirements of a quality management system in detail, the International Organization for Standardization has published a standard ISO9001:2015, the most widely used QMS standard.
Implementing the right eQMS for data and quality management improves customer satisfaction, regulatory compliance, cost of poor quality, waste reduction, and mistake proofing and even encourages a sense of purpose among teams. In short, a good quality management system, especially a fully digital and centralized one, is essential for continuous quality improvement in the life sciences.
Scilife Smart Quality Management Software has every capability a life science company needs.
Want to improve your quality management? Discover more!