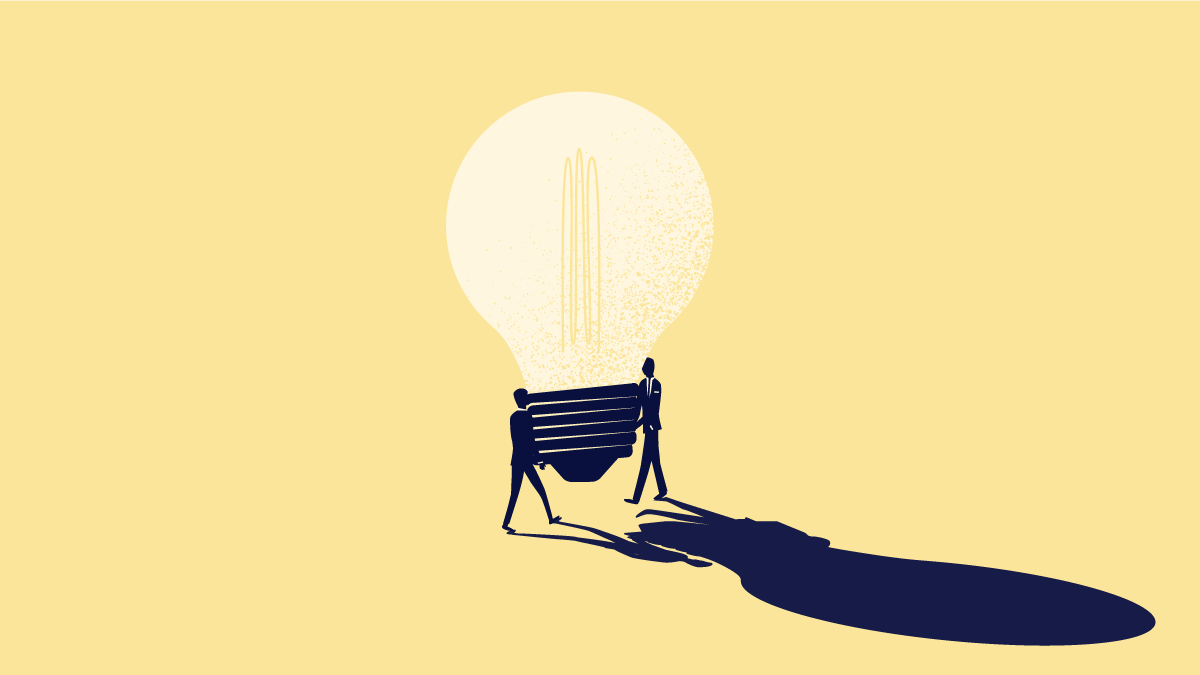
Navigating the complexities of FDA inspections is crucial for QA professionals in the pharmaceutical and medical device industries. The stakes are high, with regulatory compliance directly impacting your organization's ability to operate smoothly, avoid financial penalties, and maintain market trust. Preparation is key to success, ensuring your team is ready to meet stringent FDA requirements with confidence.
In this post, we'll explore why thorough preparation is essential for passing FDA inspections, who within your organization needs to be involved, and what specific strategies you can implement to ensure compliance. We'll cover understanding FDA regulations, preparing your inspection team, conducting internal mock inspections, maintaining document readiness, and effective communication during and after the inspection. By following these strategies, you'll be well-equipped to handle FDA inspections seamlessly, safeguarding your organization's reputation and operational integrity.
Recommended learning: If you're in the medical devices industry and want to adopt best practices tailored to your field and ensure you're always inspection-ready, check out this insightful blog!
FDA Pre-Inspection Best Practices
Understanding the regulations
The most important part of preparing for an FDA Inspection is to understand FDA regulations. You and your team should be knowledgeable about FDA regulations and always be compliant. The success originates by fostering a culture of compliance in your organization and adjusting the culture into daily operations at all levels.
The Compliance Policy Guides (CPGs) that detail the steps involved in each type of inspection, therefore make sure you review corresponding sections of CPGs and are prepared for what type of documentation will be required, as well as the time of inspection that would take.
If you follow those CPGs, your FDA inspection will be much more successful.
Understand the FDA inspection process
To understand the FDA inspection process, and what the FDA inspectors expect from organizations, you can take a look at the FDA’s website which contains a set of Inspection Guides specific for each industry that are useful in preparation for inspections. Additionally, they contain reference material that the Inspectors will use during the inspection.
Furthermore, you should know the different FDA inspection types. The FDA conducts several types of inspections however the goal is the same for all types: protect patients and consumers from unsafe products.
Designate an inspection team
FDA inspectors expect to have a key person (typically QA or RA head) who leads the inspection team of key personnel. Therefore, you should designate the key person and the inspection team before the inspection.
The inspection team consists of Subject Matter Experts (SMEs) of each area and you should ensure that all SMEs are confident in their abilities to engage with the inspectors and are well prepared to discuss any areas of concern that may arise. Additionally, all personnel especially SMEs are fully trained on the procedure required to complete their tasks, and training records are up to date, reviewed, and readily available during the inspection.
The key person is responsible for accompanying the inspectors in the course of the inspection and also should have the knowledge and authority required to speak to any concerns or requests that may arise.
Conduct internal mock FDA inspections: Perfect comes from practice
Mock FDA inspections are one of the best ways to spot and address compliance gaps before the FDA Inspection.
It simulates a real-life experience to assess an organization's preparedness. It also supports your team's ability to engage investigators by practicing their roles as an auditee and highlights any gaps that require immediate correction. Even though it’s usually conducted internally, it would be better to hire an unbiased professional who can replicate the real process accurately.
Make a plan
Train your personnel – especially the quality team – in advance and know when and how to act in response to an FDA Inspector. The best way to acknowledge your team is to have an inspection SOP that covers every aspect of an FDA inspection.
Best Practices During an FDA Inspection
Document readiness
It will be possible to prepare all documents ahead of time if the inspection is planned. In some cases, the FDA may arrive without notice. When this happens, notify all employees, especially those who might be affected, immediately so they can follow company protocol as outlined in your SOPs.
Regardless of the type of inspection, here’s a list of documents you should be prepared to provide when asked:
- The overview of the Quality Management including a Quality Manual if applicable
- Organizational chart
- Job descriptions and training protocol/records
- Device listings
- Responsibility matrix
Compile product complaints and CAPAs since your last inspection
Important procedures related to document/change controls, complaint handling, CAPA, etc. This is a common request from investigators, so it plays in your favor to be ready for it ahead of time. Designate someone who can clearly and completely explain the complaints as well as the process in place to handle them.
For those handling complaints electronically, you'll likely be expected to offer electronic information regarding them. While you may be asked for more specific information, prepare the basics first: name, product, date of receipt, whether is it MDR-reportable and a summary of the issue(s) cited.
Develop an audit dossier
An audit dossier is where you collect copies of files or samples that are submitted, along with any updates provided by FDA inspectors and all other important details throughout the inspection process. This will allow you to track documents that are submitted during the audit and help you to identify and solve issues faster.
Establish open communication
The Inspection procedure should cover the general rules on how to communicate with FDA Inspectors. There are key rules you should be following when speaking with the FDA Inspectors.
- Maintain open, honest, transparent, and professional communication with the inspectors.
- Address all queries clearly and provide answers specific to what is asked with requested documentation.
- When you don’t know the answer, let them know and tell them that you will find the answer and come back as soon as possible.
- Admit to known deficiencies in advance and prepare remediation plan(s). If the FDA inspector finds those deficiencies you can show them that you’ve identified problems and have a remediation plan to fix them.
- Cooperate with FDA inspectors and do not impede their progress or engage in idle conversation.
- Be polite, avoid confrontation, and do not challenge the inspector’s understanding of regulations.
Industry guide: Learn the ins and outs of building an inspection-ready Quality Management System (QMS). This guide covers everything from understanding regulatory requirements to insider tips for implementing effective processes
FDA Post-Inspection Best Practices
Schedule a Closeout Meeting
Typically a closeout meeting is scheduled at the end of the FDA inspection to discuss observations that include company senior management, members of the Inspection Team, and all FDA inspectors.
The FDA inspector documents any compliance deviations observed during the inspection using an FDA Form 483. The contents of Form 483 are reviewed and discussed in this meeting to make sure there is a full understanding of the observations and what they mean.
Address findings (if any)
If there are any compliance deviations identified, plan the proper action(s) that you’ll take. Once you receive the FDA Form 483, you must provide a formal response to the FDA Form 483 within 15 days. The response should include the following.
- A compliance commitment statement from company management.
- A separate response addressing each observation.
- Root cause analysis and corrective and preventative actions with planned dates for each observation.
- The verification and/or monitoring method for all future corrections and a commitment to a follow-up response.
- Add evidence documents for corrections that have already been completed.
Continuous improvement
All insights, and observations collected during the inspection would be your starting point to improve your processes further. Your commitment to quality will be strengthened by learning from the experience.
Scilife Tips
By partnering with Scilife, we’ll support you to ensure all of your processes and products are aligned with applicable quality and regulatory compliance and validation requirements.
Scilife helps you to create a quality culture within your organization and improve your processes with regular internal and mock audits. Those audits are not just part of the quality management system but they are also cornerstones of continuous improvements and make your processes better from yesterday. You will navigate the FDA inspections with confidence.
Conclusion
Success in FDA inspections hinges on thorough preparation and fostering a culture of continuous improvement. By implementing these strategies, your organization can confidently navigate FDA inspections, ensuring compliance and upholding the highest standards of quality and patient safety. If you need assistance with your compliance strategy, feel free to contact us.